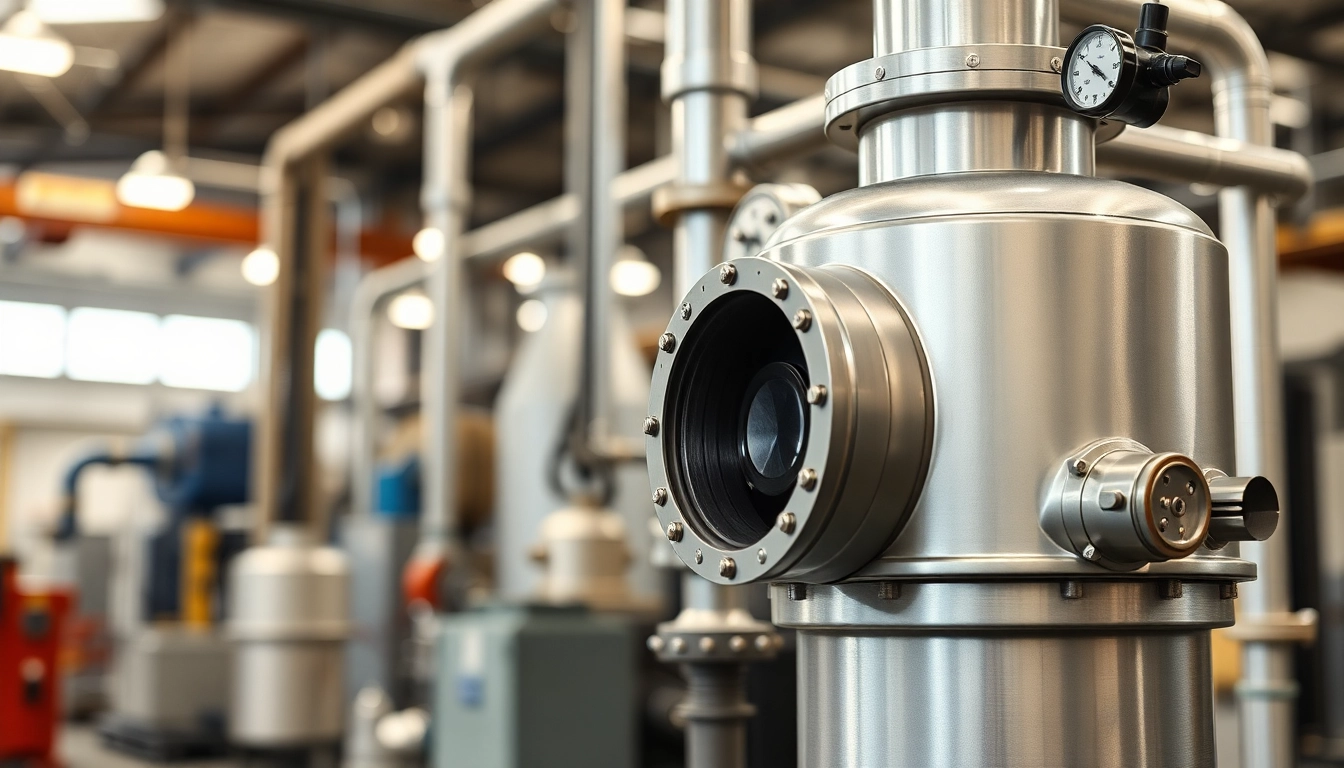
Introduction to Vacuum Ejectors
Vacuum ejectors are essential components in numerous industrial processes, known for their ability to generate a vacuum quickly and efficiently. At their core, they operate based on the Venturi effect, which allows them to convert pressure energy from a compressed fluid (typically air or steam) into a vacuum. This fascinating interaction makes them a popular choice in applications ranging from manufacturing to packaging. This article aims to provide a comprehensive overview of vacuum ejectors, exploring their functionality, variations, advantages, and future trends in design and application. For more information about vacuum ejectors, visit Vacuum ejector.
What is a Vacuum Ejector?
A vacuum ejector, sometimes referred to as an ejector or aspirator, is a pneumatic device that uses compressed air or steam to create a vacuum. Its construction typically consists of a nozzle, a suction chamber, and an exhaust port. When compressed air passes through the nozzle, it accelerates and causes a drop in pressure, creating a vacuum that allows for the suction of surrounding air or gases. These devices are favored in various applications due to their simplicity, reliability, and low maintenance requirements.
How Vacuum Ejectors Work
Vacuum ejectors operate by leveraging the principles of fluid dynamics, particularly the Venturi effect, named after Giovanni Battista Venturi, who discovered that fluid pressure decreases when its velocity increases. When compressed air enters the ejector, it flows through a converging nozzle that decreases the cross-sectional area, thus increasing the fluid velocity. The resulting low pressure in the suction chamber enables the device to draw in air, creating a vacuum. As air enters the ejector, it mixes with the high-speed jet of compressed air, then exits through the exhaust port, maintaining a continuous flow.
The Importance of the Venturi Effect
The Venturi effect is crucial to the functionality of vacuum ejectors. It explains the relationship between velocity and pressure that underpins their operation. By utilizing this effect, vacuum ejectors can generate a vacuum without the need for moving parts, which significantly reduces wear and potential failures. This characteristic makes them suitable for a wide array of industrial applications, including material handling and environmental cleanup, where reliable vacuum generation is key.
Types of Vacuum Ejectors
Single-Stage vs. Multi-Stage Vacuum Ejectors
Vacuum ejectors generally fall into two categories: single-stage and multi-stage varieties. Single-stage ejectors are simpler; they use a single nozzle to achieve the desired vacuum level. These are typically more cost-effective and easier to maintain. Multi-stage ejectors, on the other hand, consist of several sequential nozzles, allowing for greater vacuum levels and capacity by utilizing the exhaust from one stage as the input for the next. While they can be more expensive and complex to install, multi-stage ejectors can efficiently handle a higher volume of gases or air, making them suitable for demanding industrial applications.
Common Applications of Vacuum Ejectors
Vacuum ejectors find their way into a broad spectrum of industrial applications. Some common uses include:
- Packaging: Vacuum ejectors play a key role in food and product packaging, helping to minimize oxygen exposure and extend shelf life.
- Material Handling: In manufacturing, vacuum ejectors assist in moving lightweight materials, enhancing productivity and safety.
- Environmental Cleanup: Vacuum ejectors can be used in systems designed to remove contaminated air or fluids, supporting environmental remediation efforts.
- Printing and Visualization: They are often employed in processes requiring precise handling of substrates, ensuring optimal separation and support.
Specialized Ejector Designs
Over time, specialized designs of vacuum ejectors have emerged to cater to specific industry needs. For instance, water aspirators utilize water flow instead of air to create a vacuum, making them ideal for lab applications where contamination risk must be minimized. Furthermore, steam ejectors harness the power of steam to produce vacuum, often used in chemical processes where high temperatures are involved. This diversity enables engineers and designers to select the most suitable ejector for their specific requirements.
Advantages of Using Vacuum Ejectors
Efficient Vacuum Generation
One of the primary advantages of vacuum ejectors is their efficiency in vacuum generation. Unlike mechanical pumps that can become cumbersome, vacuum ejectors offer quick response times and consistent performance. Their capability to maintain a vacuum with minimal power consumption makes them an attractive option in energy-sensitive applications.
Cost-Effectiveness and Maintenance
Vacuum ejectors are celebrated for their cost-effectiveness. Due to their simple design and lack of moving parts, they typically involve lower installation and maintenance costs compared to traditional vacuum pumps. This simplicity also translates into longer lifespans, allowing businesses to maximize their return on investment. Additionally, as vacuum ejectors are often used in various industries, they can be readily integrated into existing systems without significant retrofitting.
Space-Saving Solutions in Design
In today’s industrial landscape, space is often at a premium. Vacuum ejectors excel in providing a compact alternative to traditional vacuum systems. Their small footprint allows for easier integration into confined spaces, facilitating streamlined operations while maintaining high levels of performance. This compactness is particularly advantageous in automated systems, where overhead and layout considerations are critical.
Implementing Vacuum Ejectors in Systems
Best Practices for Installation
To ensure the optimal performance of vacuum ejectors, it is vital to follow best practices during installation. This includes:
- Correct Sizing: Selecting the right size ejector for your application based on desired vacuum levels and throughput requirements is crucial.
- Adequate Filtration: Implementing effective filtration systems upstream of the ejector can prevent contamination and prolong its lifespan.
- Proper Orientation: Installing ejectors in their recommended orientation can minimize performance issues and enhance overall functionality.
- Regular Maintenance: While vacuum ejectors are generally low-maintenance, periodic inspection and cleaning of filters and exhaust ports is essential for sustained effectiveness.
Common Challenges and Solutions
While vacuum ejectors are robust devices, users may encounter certain challenges, such as:
- Pulsation and Fluctuations: Variations in suction pressure can occur if the ejector is improperly sized or if the compressed air supply fluctuates. It is essential to ensure a stable air supply and consider multi-stage designs if necessary.
- Noise Levels: Vacuum ejectors can generate significant noise due to high airflow velocities. Utilizing silencing devices or installing the ejector away from sensitive areas can mitigate this issue.
- Maintenance Complexity: Although generally low-maintenance, issues may arise if a filter is clogged. Regular inspections and the use of easy-access filter housings can streamline maintenance operations.
Performance Metrics to Consider
When evaluating vacuum ejectors, several performance metrics should be taken into account:
- Vacuum Level: The capacity of an ejector to produce a specific vacuum level is paramount for effective operation.
- Flow Rate: The volume of air or gas that the ejector can handle is vital for ensuring it meets the demands of the application.
- Power Consumption: Analyzing the energy requirements of the ejector can assist in determining operational costs and efficiency.
- Response Time: The time it takes for the ejector to reach optimal performance after activation can influence the overall efficiency of the process it supports.
Future Trends in Vacuum Ejector Technology
Innovations in Ejector Design
The field of vacuum ejector technology is continually evolving, with ongoing innovations aimed at improving efficiency and functionality. For instance, manufacturers are exploring materials that reduce wear and corrosion, enhancing the longevity and performance of ejectors. Additionally, computational fluid dynamics (CFD) is increasingly being utilized in the design stage to optimize shapes and sizes for improved performance, resulting in more effective ejectors with higher vacuum levels.
Impact of Industry 4.0 on Vacuum Systems
As Industry 4.0 and automation reshape manufacturing, vacuum ejectors are also benefiting from smart technology. Integrated sensors and IoT connectivity allow for real-time monitoring and diagnostics, enabling predictive maintenance and reducing downtime. This shift not only enhances operational efficiency but also contributes to smarter energy management and sustainability practices within facilities.
Environmental Considerations and Efficiency
With the increased focus on sustainability, the future of vacuum ejector technology will likely focus on reducing energy consumption and promoting eco-friendly designs. Innovations aimed at minimizing air leaks and optimizing the use of compressed air can significantly enhance the overall environmental performance of suction systems. Furthermore, integrating vacuum ejectors with renewable energy sources could help decrease reliance on traditional power grids.