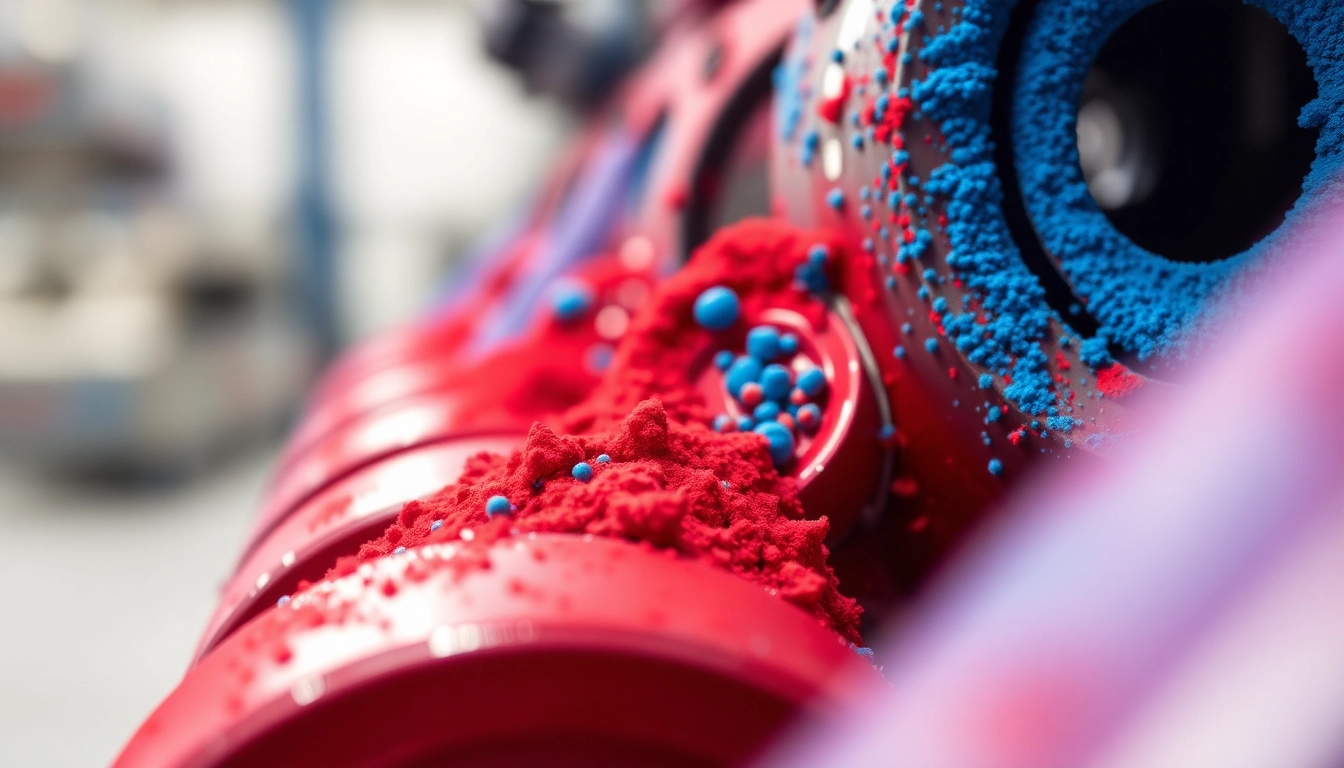
Understanding Powder Coating Basics
What is Powder Coating?
Powder coating is a dry finishing process that creates a hard and durable layer on metal surfaces, widely used for various applications, including automotive, appliances, and industrial materials. Instead of liquid paint, which relies on solvents to keep the pigments in a liquid state, powder coating consists of finely ground particles that are electrostatically charged and then sprayed onto a surface. This process allows for a uniform layer that adheres smoothly over complex geometries.
Unlike traditional paint, the powder form allows for a much thicker coating without running or sagging, achieving a smoother finish. Once applied, the electrostatically charged powder is heated in an oven, causing it to melt and cure into a solid film that bonds strongly to the substrate, providing enhanced protection and aesthetic appeal. A deeper dive into powder coating processes can reveal insights into how it surpasses some conventional painting methods.
How Powder Coating Works
The powder coating process involves several crucial stages: preparation, application, and curing. Initially, surfaces must be cleaned thoroughly to remove any contaminants, such as grease or rust, which could interfere with adhesion. Once prepped, the surface is grounded, and a powder coating gun is used to spray the powder onto the surface. This gun imparts an electrical charge to the powder particles, which then are attracted to the grounded object, ensuring uniform coverage.
After application, the coated item is placed in a curing oven, where heat activates the curing agents in the powder. This process can range from 10 to 30 minutes depending on the ingredients of the powder and the material being coated. The heat causes the powder particles to fuse and form a solid layer, resulting in a durable, attractive finish that often surpasses traditional paint in longevity and durability.
Types of Powder Coating Materials
There are two primary types of powder coatings: thermosetting and thermoplastic. Thermosetting powders, such as epoxy and polyurethane, cure when heated and cannot be remelted, providing excellent durability and corrosion resistance. They are ideal for applications requiring strong, resilient finishes, such as automotive and industrial coatings.
On the other hand, thermoplastic powders can be melted and remolded multiple times, allowing for easier repairs and touch-ups but offering lower heat resistance compared to thermosettings. Additionally, within these categories, there are various formulations, including matte, glossy, and textured finishes, catering to different design needs and aesthetic preferences.
Benefits of Choosing Powder Coating
Durability and Protection Offered by Powder Coating
One of the primary advantages of powder coating is its impressive durability. The finished product is often more resistant to scratches, chipping, and corrosion, outlasting conventional paint jobs, which tend to wear due to environmental exposure and usage. This durability means items coated with powder sustain their finish longer, leading to lower maintenance costs over time.
In particular, powder coating endures well against harsh weather conditions, making it an optimal choice for outdoor applications such as patio furniture and automotive parts. Additionally, the UV resistance inherent in certain powder formulations helps prevent fading, ensuring colors remain vibrant for years.
Aesthetic Appeal and Color Variety in Powder Coating
Powder coating offers a vast palette of colors and finishes, providing flexibility in design that can’t be matched by traditional paint. Manufacturers and customers alike can choose from an array of textures, gloss levels, metallic finishes, and even custom colors, allowing them to achieve exactly the look they desire.
Furthermore, advancements in powder coating technologies have ushered in innovative options such as multicolored effects and even specialty powders that change color with temperature. These options not only enhance visibility for branding or identity but also serve functional purposes, fulfilling specific requirements for aesthetic appeal.
Environmental Impact and Safety of Powder Coating
From an environmental perspective, powder coating is more advantageous than traditional liquid paints. The process generates minimal waste, as any overspray can be collected and reused, greatly reducing overall material waste. Additionally, powder coating does not release volatile organic compounds (VOCs), which can contribute to air pollution and health hazards. This environmentally friendly aspect aligns with growing consumer demand for sustainable manufacturing practices.
Moreover, since powder coating is non-toxic and often contains fewer hazardous agents than conventional paint, it’s a safer option both for workers handling the materials and for end-users at home.
Powder Coating Process Explained
Preparation Steps for Powder Coating
The success of powder coating hinges on meticulous preparation of the substrate. This generally includes processes such as abrasive blasting, solvent degreasing, and chemical treatments to ensure maximum adhesion. Thorough cleaning is essential; otherwise, contaminants can lead to poor bonding and an unsatisfactory finish.
Once cleaned, items should be thoroughly wiped down or air-blasted to remove any residual cleaning agents. For some applications, applying a primer before powder coating may also enhance adhesion and prolong the lifespan of the coating.
Application Techniques for Powder Coating
After preparation, the surface is now ready for the application of powder. The powder is transferred from a hopper to a powder coating gun, which uses electrostatic charge to distribute the powder evenly across the surface. The gun’s nozzle shape and movement speed can be adjusted to control the thickness and consistency of the coating.
Spray booths are often employed to minimize contamination during this process, while most professionals wear protective gear to ensure safety from inhaling any powder. Manual application techniques often used in smaller operations involve hand-held powder spray guns, while larger operations may use Automated Application Equipment to achieve consistent results at higher production rates.
Curing Process in Powder Coating
Once applied, powder-coated objects are placed in curing ovens set to specific temperatures, typically between 350°F and 400°F. The precise curing time depends on the thickness of the powder and the substrate material but generally ranges from 10 to 30 minutes. During curing, the powder melts and chemically bonds to the substrate, ensuring that the final coating has an excellent surface profile and enhanced resistance to wear and impact.
Following curing, items are cooled gradually to guarantee that the coating remains intact and free of defects. This final touch is crucial for achieving optimal performance and appearance.
Common Applications of Powder Coating
Powder Coating in Automotive Industries
The automotive sector widely embraces powder coating for both aesthetic and protective applications. From vehicle frames to wheels, powder coatings are favored for their durability and colorful options. Typically, car manufacturers use powder coatings on various components—everything from automotive trim to exhaust systems, seeking finishes that withstand high temperatures and the rigors of daily use.
High-performance powder coatings are also employed for bodywork that requires resistance to chipping and scratching, ensuring vehicles maintain their look despite road wear.
Uses of Powder Coating in Home Appliances
Home appliance manufacturers often choose powder coating for metal parts because of the durability it offers against constant usage, scratches, and cleaning agents. Refrigerators, stoves, and even dishwashers frequently feature powder-coated surfaces as they maintain a fresh appearance over time without succumbing to the usual wear and tear.
In addition, the availability of various coatings makes it easier for manufacturers to produce appliances that not only resist fingerprints and stains but also blend seamlessly with modern décor.
Metal Fabrication and Powder Coating Solutions
Metal fabrication companies also frequently rely on powder coating due to its ability to enhance the protective features of finished products while adding an attractive finish. Metals used in outdoor furniture, machinery, and structural applications benefit significantly from powder coatings’ resilience against corrosion and harsh environmental conditions.
Moreover, custom fabricators can offer clients tailored solutions by employing various powder types to meet specific operational demands, thus maximizing both appeal and functionality.
Tips for Choosing the Right Powder Coating Service
Evaluating Powder Coating Providers
When selecting a powder coating provider, it’s crucial to assess their capability and reputation in the industry. Seek candidates with a robust portfolio that illustrates their experience and expertise in various applications. Checking reviews and testimonials from previous clients can provide valuable insights into their reliability and quality.
Additionally, consider asking potential providers about their equipment and technologies. A modern facility with updated machinery is often indicative of better quality control and consistency in output.
Key Questions to Ask About Powder Coating Services
Before finalizing a provider, it’s vital to inquire about several key factors:
- What types of powder do they use, and can they accommodate custom colors?
- What preparation and cleaning processes do they perform on your items before coating?
- What is their turnaround time based on your quantity and complexity of the job?
- Do they offer any warranties or guarantees on their coatings?
- Can they provide samples or references from similar projects?
Understanding Cost Factors in Powder Coating
The cost of powder coating can vary based on several aspects such as the type of powder used, surface preparation requirements, volume of items, and curing times. Generally, many services charge based on surface area, so larger or more complex items will incur higher costs.
While cheaper services may be tempting, it’s crucial to weigh costs against quality and durability of the finished product. Investing in a reliable powder coating service can save money in the long run by reducing maintenance and replacement costs.