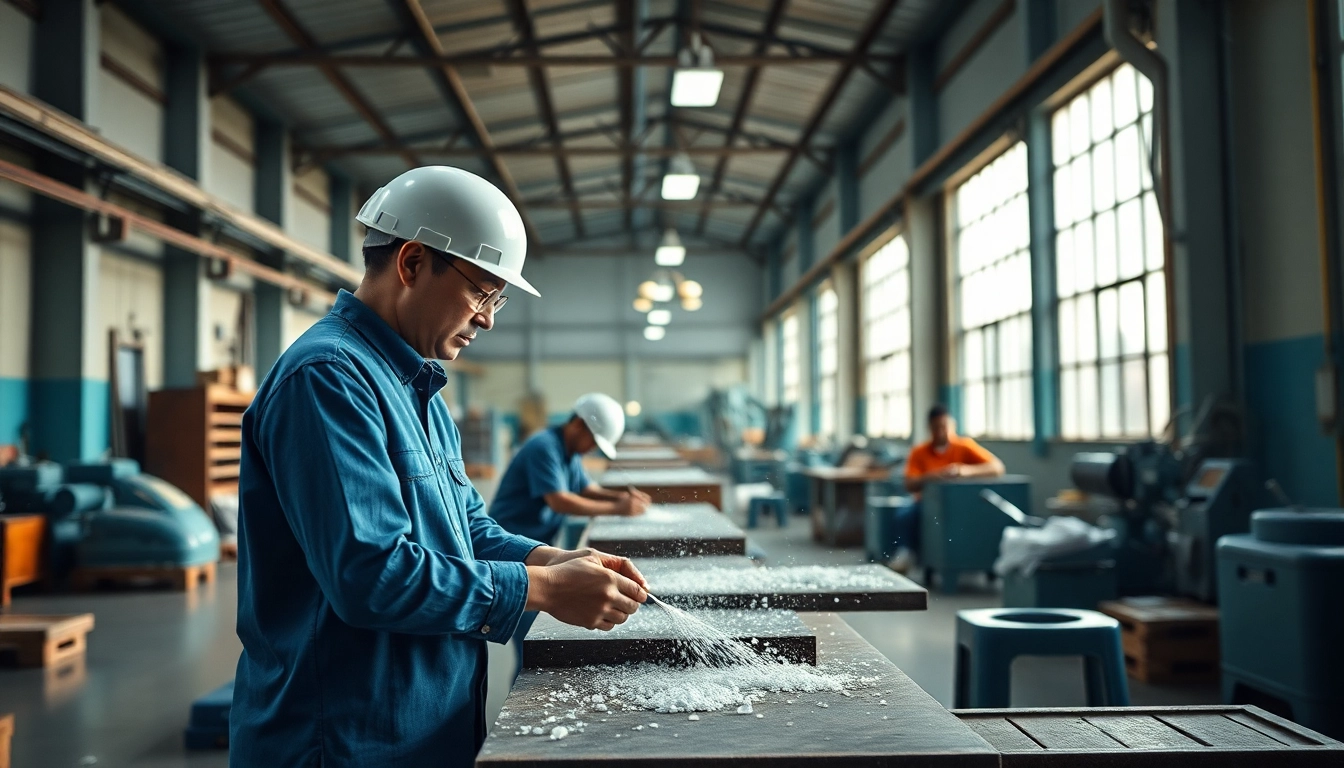
Understanding Liquid Packaging Machines
Definition and Importance
Liquid packaging machines are specialized devices designed to handle the packaging of liquid products. These machines play a crucial role in various industries, including food, pharmaceuticals, chemicals, and cosmetics. Their primary function is to automate the filling, sealing, and labeling processes, ensuring that products are packaged efficiently and safely. As a result, they not only enhance productivity but also maintain the quality and integrity of the packaged liquids.
The importance of liquid packaging machines extends beyond mere efficiency. They are integral to meeting regulatory standards and ensuring product safety. For manufacturers, investing in reliable Liquid Packaging Machine Supplier solutions translates to reduced operational costs, improved output quality, and greater customer satisfaction.
Key Components of Liquid Packaging Machines
Understanding the key components of a liquid packaging machine is essential for evaluating its efficiency and suitability for specific applications. Here are the primary components:
- Filling System: This is the heart of the liquid packaging machine. It determines the filling speed and accuracy. Various technologies such as piston fillers, pump fillers, and gravity fillers are used based on the liquid’s viscosity.
- Cap Sealing Mechanism: Ensuring that containers are properly sealed prevents leaks and contamination. Types of closures include screw caps, snap-on caps, and heat seals, each requiring specific sealing technologies.
- Labeling Station: A labeling station adheres labels to the containers, which can be crucial for branding and regulatory compliance.
- Conveyor System: This component automates the movement of containers through the machine, increasing overall efficiency and reducing manual labor.
- Control Panel: Modern machines come equipped with an intuitive control panel, allowing operators to set parameters, monitor performance, and troubleshoot issues effectively.
Types of Liquid Packaging Machines
Liquid packaging machines can be categorized based on their design, functionality, and the types of products they handle. Here are the main types:
- Automatic Filling Machines: These machines offer continuous production capabilities and are ideal for high-volume operations. They can handle various liquid types, from water to thick sauces.
- Semi-Automatic Filling Machines: These machines require some manual intervention, making them suitable for facilities with lower production demands.
- Vertical Form Fill Seal (VFFS) Machines: Common in the food industry, VFFS machines are designed to create bags from roll stock, fill them with liquids, and seal them in a continuous process.
- Horizontal Form Fill Seal (HFFS) Machines: These are versatile machines used for larger, flat packages, commonly used for pouches and sachets.
- Bottle Filling Machines: Specialized to fill rigid containers, these can be equipped with various filling technologies to ensure accuracy and speed.
Choosing the Right Liquid Packaging Machine Supplier
Evaluating Supplier Capabilities
When selecting a supplier for liquid packaging machines, it’s imperative to assess their capabilities logically and systematically. Potential suppliers should have proven expertise in their field, evidenced by their product range and technological advancements. Look for a supplier whose product offerings are tailored to meet specific industry needs and who can provide additional services such as installation, training, and maintenance.
Also, check the supplier’s manufacturing standards and certifications (such as ISO). This ensures you are dealing with a reputable entity committed to quality. Request sample cases or machine demonstrations to witness their products in action, allowing you to evaluate performance and ease of use.
Assessing Customer Reviews and Reputation
Before committing to a supplier, it is advisable to conduct thorough research on their reputation. Customer reviews often serve as a reliable source for assessing the reliability and service levels a supplier offers. Look for reviews across various platforms—including their website, third-party product review sites, and industry forums—to get a well-rounded perspective.
Furthermore, consider reaching out to existing clients or industry peers to gather first-hand experiences of their interactions with the supplier. A company with a strong reputation for customer service will typically have satisfied customers who are willing to recommend them.
Understanding Industry Experience
The level of experience a supplier has in the liquid packaging machinery sector can significantly impact the performance of the equipment they provide. Suppliers with extensive industry experience are more likely to understand the challenges faced by different sectors and can offer better insights into which machine configurations will work best for specific applications.
Additionally, seasoned suppliers will be more able to provide proven solutions and troubleshooting expertise, ensuring that your operations run smoothly and effectively.
Benefits of Advanced Packaging Solutions
Enhanced Efficiency and Speed
One of the most significant benefits of implementing advanced liquid packaging solutions is improved efficiency. Automating the packaging process reduces manual labor costs and minimizes human errors, meaning that products can be packaged faster and with greater accuracy. With modern machines capable of handling numerous containers per minute, businesses can significantly increase their output.
For example, a bottling company that invests in automatic filling and capping machines may see output increase from a few hundred bottles per hour to several thousand, depending on the machine’s specifications and the product type, leading to a substantial boost in productivity.
Cost-Effectiveness Over Time
While the initial investment for advanced liquid packaging machinery can be substantial, the long-term savings often outweigh these costs. With less downtime, reduced labor requirements, and minimal waste, companies can enjoy increased profit margins. The longevity and durability of modern machines also mean that businesses spend less on repairs and replacements over time.
Moreover, energy-efficient models are becoming increasingly prevalent, contributing to reduced energy bills. Companies that invest in sustainable technology often enjoy the added benefit of enhanced brand reputation and compliance with environmental regulations.
Compliance with Industry Standards
Adhering to safety and quality standards is non-negotiable in the packaging industry, particularly in sectors like food and pharmaceuticals. Advanced liquid packaging solutions are designed to keep up with these stringent regulations, offering features such as automated quality checks and traceability systems that help companies maintain compliance with local and global standards.
For instance, manufacturers of pharmaceutical products must follow stringent guidelines regarding cleanliness and contamination prevention. Advanced machines that incorporate these safety features into their design aid in meeting such regulatory requirements while ensuring the integrity of the sealed product.
Customization Options for Liquid Packaging
Adapting Machines to Specific Products
One of the critical advantages of engaging with leading liquid packaging machine suppliers is the opportunity for customization. Different products, especially in the liquid category, require tailored approaches for optimal packaging. For example, thick substances like sauces might need piston fillers, while thinner liquids like water can be efficiently filled using gravity or pump systems.
Customizable features could include altering the filling volume, modifying the container type, and even adjusting the machinery’s speed and output rates. This flexibility enables businesses to adapt quickly to changing market demands or launch new products without needing to entirely revamp their existing processing line.
Flexible Design for Various Container Types
Modern liquid packaging machines are often designed with versatility in mind. They can efficiently handle a range of container types, including bottles, pouches, and cartons. This flexibility is particularly important for businesses looking to diversify their product offerings without investing heavily in new machinery.
For instance, a manufacturer might wish to shift from filling plastic bottles to glass containers. A machine capable of accommodating different formats will facilitate this transition without requiring significant downtime or retrofitting.
Integration of Technology in Packaging
The integration of cutting-edge technology into liquid packaging machinery enhances efficiency, accuracy, and reliability. Features such as Internet of Things (IoT) connectivity, machine learning, and real-time monitoring systems allow for proactive maintenance and operational monitoring. This integration not only optimizes the packaging process but also aids in resource management and planning.
Furthermore, the implementation of smart sensors can enhance quality control by detecting irregularities in the filling process, providing feedback to adjust settings in real time. Such advancements ensure high-quality packaging and improve overall operational reliability.
Future Trends in Liquid Packaging Machinery
Innovation in Automation
Automation continues to evolve within the liquid packaging industry, with an increasing number of manufacturers implementing advanced robotic technologies to streamline operations. Automated machines can perform repetitive tasks more efficiently and with higher precision than human labor, significantly reducing labor costs and error rates.
Emerging technologies, such as artificial intelligence, will further enhance the automation of liquid packaging processes, allowing for smarter systems that can learn from operational data and optimize themselves over time. The move toward full automation not only benefits efficiency but also allows for better scalability in production, accommodating varying demand levels without substantial changes to processes.
Sustainability Practices in Packaging
Sustainability has become a core concern across industries, and the liquid packaging sector is no exception. Modern packaging solutions are increasingly focusing on reducing waste and employing eco-friendly materials. Suppliers are innovating by creating machinery that utilizes biodegradable packaging materials and energy-efficient manufacturing processes.
Incorporating sustainability into liquid packaging not only meets regulatory pressures but also caters to a growing consumer base that prioritizes environmentally responsible practices. Companies that adopt these practices can distinguish themselves in a crowded marketplace and foster stronger brand loyalty among environmentally conscious consumers.
Emerging Technologies to Watch
The liquid packaging industry is likely to see an influx of new technologies that promise to revolutionize operations. Key trends include advanced analytics for predictive maintenance, machine learning for process optimization, and blockchain technology for enhanced transparency and traceability in supply chains.
As businesses lean more into digital transformations, the adoption of such emerging technologies will not only allow them to optimize their processes but also respond more agilely to market demands, consumer preferences, and regulatory requirements.