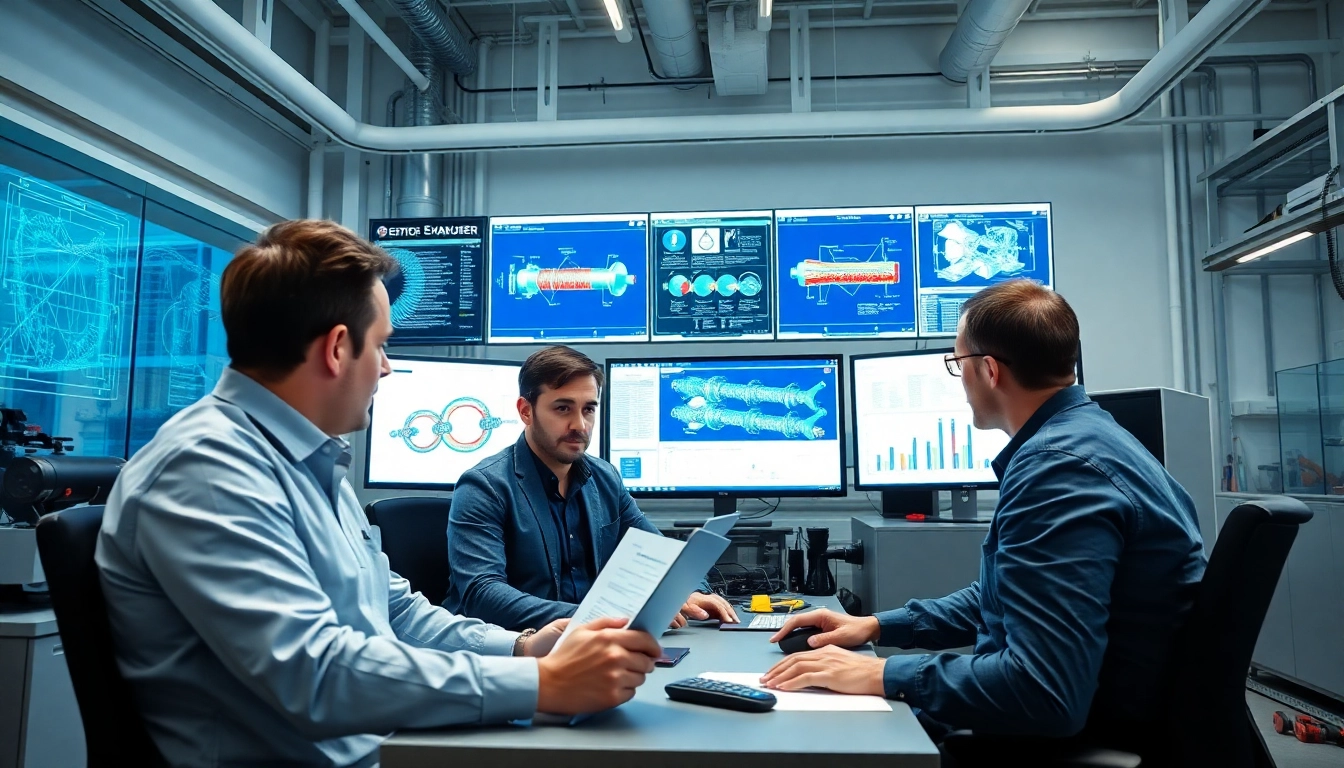
Understanding Pipe Stress Analysis
What is Pipe Stress Analysis?
Pipe stress analysis is a crucial process in engineering that evaluates the stresses, deflections, and overall behavior of piping systems under various operating conditions. Typically employed in industries such as oil and gas, chemical processing, shipbuilding, and power generation, this analysis ensures that piping systems can support their operational demands while maintaining integrity and safety.
At its core, pipe stress analysis assesses how pipes react to changes in temperature, pressure, weight, and other external forces, such as wind or seismic activity. By analyzing these stress factors, engineers can predict potential failures, thereby mitigating risks and enhancing system longevity.
Importance in Engineering Design
The significance of pipe stress analysis extends beyond mere compliance with safety standards. It plays a pivotal role in optimizing system design to avoid excessive wear and tear, reduce maintenance costs, and enhance operational efficiency. By identifying stress points in the design phase, engineers can make informed choices regarding material selection and pipe routing, leading to robust and cost-effective solutions.
Furthermore, as systems become more complex and the demand for higher pressures and temperatures increases, the necessity for thorough analysis grows. Integrating pipe stress analysis early in the design process can prevent costly retrofits and operational downtimes in the future.
Common Challenges in Pipe Stress Analysis
Despite its importance, there are numerous challenges in conducting effective pipe stress analysis. One of the primary difficulties lies in accurately modeling complex configurations and load scenarios, especially when dealing with non-linear behaviors. Additionally, varying material properties and environmental conditions add layers of complexity to the analysis.
Another challenge is the need for continuous monitoring and verification. As systems are subject to wear over time, initial analysis results may no longer reflect the current state of the piping. Thus, engineers must adopt a proactive approach to continually assess and ensure the reliability of piping systems.
Key Principles of Pipe Stress Analysis
Types of Stress in Piping Systems
In the context of piping systems, stresses can be broadly categorized into several types:
- Tensile stress: Caused by pulling forces acting on the pipe.
- Compressive stress: Emerges from forces that push inward toward the pipe.
- Bending stress: Develops when external loads create a moment that bends the pipe.
- Shear stress: Results from forces sliding parallel along the material.
- Thermal stress: Occurs due to expansion or contraction in response to temperature changes.
Understanding these stresses is vital for determining whether the materials and design will withstand operational demands over time.
Factors Affecting Pipe Stress
Several factors influence pipe stress, including:
- Temperature fluctuations: Rapid changes can lead to expansion or contraction, causing significant stress.
- Pressure changes: Variations in internal pressure can lead to stress and potential failure.
- Weight of the pipe and contents: Heavier materials may reduce the system’s allowable load limits.
- Support conditions: The method of supporting the pipes can create stress concentrations.
Each of these factors must be carefully considered during the analysis to ensure the robustness of the design.
Code Compliance and Standards
Compliance with industry codes and standards is paramount in pipe stress analysis. Organizations such as the American Society of Mechanical Engineers (ASME), the American Petroleum Institute (API), and the International Organization for Standardization (ISO) provide guidelines that help engineers design safe and efficient piping systems.
Adhering to these codes not only enhances safety and reliability but also minimizes liability risks for companies. Regular updates to these standards mean that engineers must remain informed about best practices and legislative changes impacting pipe stress analysis.
Tools and Software for Pipe Stress Analysis
Overview of Popular Analysis Tools
A plethora of tools and software packages are available for conducting pipe stress analysis, each with unique features designed to aid engineers in evaluating piping systems. Some popular tools include:
- CAESAR II: A widely used program that allows for detailed stress and flexibility analysis of piping systems.
- ANSYS: Provides advanced simulation capabilities, including thermal and vibrational analysis.
- AutoPIPE: Focused on optimizing design with integrated calculations for stress, support reactions, and thermal effects.
- SolidWorks Simulation: Useful for general stress analysis as part of a broader CAD design environment.
These tools greatly enhance the ability to visualize and quantify stress profiles, leading to informed design decisions.
Evaluating Software Features
When choosing a tool for pipe stress analysis, it’s essential to consider a few key factors:
- User interface: An intuitive interface can greatly improve ease of use and reduce training time.
- Customization and flexibility: The ability to modify the software to fit specific project needs is crucial.
- Support and updates: Regular software updates and responsive customer support can enhance usability and address challenges quickly.
- Integration capabilities: Seamless integration with CAD systems and other engineering tools can streamline workflows.
By evaluating these features, engineers can select software that not only meets their immediate needs but also adapts to future project complexities.
Best Practices for Implementation
To maximize the effectiveness of pipe stress analysis tools, consider the following best practices:
- Standardization of processes: Creating standardized procedures for analysis can promote consistency and improve outcomes.
- Continuous training: Regular training sessions for engineers ensure that they stay updated on software capabilities and analysis techniques.
- Regular reviews and audits: Periodically reviewing designs and analyses can catch potential issues early in the design process.
- Integrated approach: Collaborating with structural engineers and other disciplines can provide a holistic view of the system’s performance.
Implementing these best practices fosters a culture of safety and reliability in piping design.
Case Studies in Pipe Stress Analysis
Real-World Applications
To emphasize the practical importance of pipe stress analysis, we can look at several case studies where effective analysis played a crucial role.
For example, in a recent offshore oil platform project, engineers needed to design piping systems that could withstand high wave impacts and fluctuating temperatures. Using advanced simulation software, they fed environmental data into their analysis, allowing them to optimize pipe layouts and support systems. The successful implementation not only preserved the integrity of the pipes but also reduced installation costs and improved safety metrics.
Lessons Learned from Failures
Failures in piping systems often result in significant operational disruptions and financial losses. One notorious incident involved a natural gas pipeline that ruptured due to inadequate thermal stress analysis. The analysis did not account for severe temperature fluctuations, which led to excessive pipe deformation and ultimately failure. This incident highlights the necessity of rigorous, ongoing stress analysis to adapt to changing conditions, advocating for a re-evaluation of existing systems rather than relying solely on initial assessments.
Success Stories in Pipe Design
Conversely, organizations that employ robust stress analysis methodologies tend to experience better outcomes. A chemical processing plant integrated pipe stress analysis into their routine assessments, leading to an innovative redesign of their piping system. With accurate stress calculations, they implemented a pipeline layout that not only reduced material use but also extended the lifecycle of their installation. This proactive approach demonstrates the long-term value that effective analysis can bring to any piping project.
Future Trends in Pipe Stress Analysis
Advancements in Simulation Technology
The landscape of pipe stress analysis is evolving rapidly, with new simulation technologies emerging to enhance accuracy and efficiency. Advanced finite element analysis (FEA) tools are becoming more prevalent, allowing engineers to simulate real-world scenarios with greater fidelity. These simulations can take into account a multitude of variables simultaneously, providing insights that were previously unattainable.
Moreover, the integration of 3D modeling into stress analysis processes improves the accuracy of geometric representations, resulting in more reliable outputs. This shift towards comprehensive modeling will support the development of more complex systems safely and effectively.
Predictive Analysis Using AI
Artificial intelligence (AI) is set to revolutionize pipe stress analysis in the coming years. Through machine learning algorithms, AI can analyze large datasets to predict potential failures before they occur. By identifying patterns associated with previous failures, AI can recommend design alterations that mitigate risks. The incorporation of AI into stress analysis processes promises to enhance operational safety and reduce downtime significantly.
Regulatory Changes and Their Impact
As industries evolve and new materials emerge, regulatory bodies consistently update standards related to pipe stress analysis. Staying abreast of these changes is vital for engineers, as non-compliance can result in severe penalties and increased safety risks. Consequently, organizations must cultivate a proactive approach to regulatory shifts by integrating them into their design and analysis processes.
In conclusion, the future of pipe stress analysis will undoubtedly be shaped by technological advancements and changing regulations. By embracing innovative tools and staying current with industry developments, engineers can continue to ensure the safety, reliability, and efficiency of piping systems across various sectors.