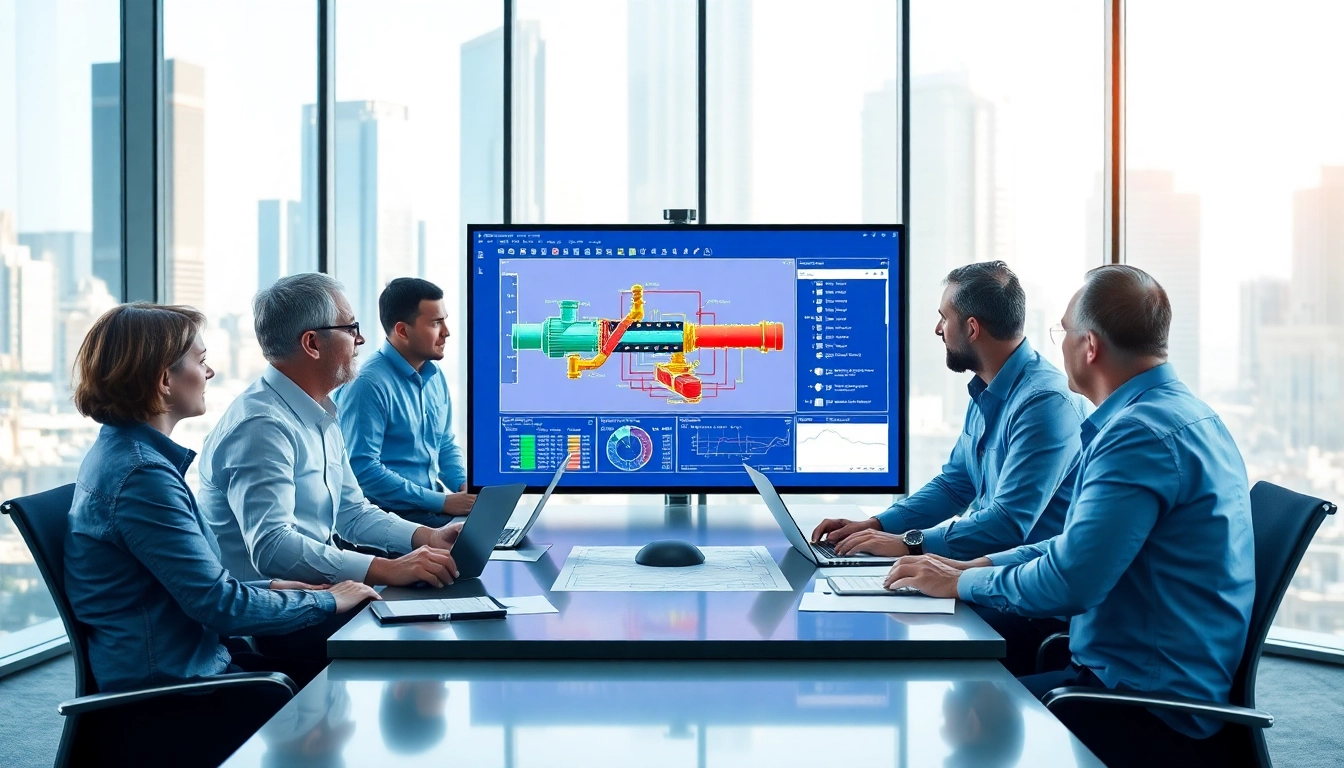
Understanding Pipe Stress: An Essential Component of Engineering
In the world of engineering, particularly in the design and operation of piping systems, understanding the stresses that pipes endure is crucial. Pipe stress analysis is a vital process that ensures the integrity and longevity of piping systems used across various industries, from oil and gas to water distribution. A pipe stress Company plays a pivotal role in facilitating this analysis, helping organizations mitigate potential risks and enhance operational efficiency.
What is Pipe Stress Analysis?
Pipe stress analysis is a method used to determine the stresses and deflections in piping systems subjected to various forces. These forces may arise from thermal expansion, weight, pressure, and other external loads. The analysis helps engineers understand how these stressors affect the performance and safety of the pipes.
The ultimate goal is to ensure that the piping can withstand the operational environment without failure. Engineers employ various computational techniques and software tools to simulate stress conditions, allowing them to predict potential issues and make informed design decisions.
The Role of a Pipe Stress Company in Industry
A pipe stress company specializes in assessing and optimizing piping systems to ensure they comply with industry standards. These companies bring a wealth of expertise, employing trained professionals equipped with advanced analytical tools. They can effectively troubleshoot existing systems and anticipate challenges that may arise in future projects.
Furthermore, they provide detailed documentation and reports that can serve as a reference for regulatory compliance and future maintenance. This expertise is essential, particularly in high-stakes industries where even minor errors can lead to catastrophic failures.
Common Applications and Industries of Pipe Stress Analysis
Pipe stress analysis is employed across various sectors, including:
- Oil and Gas: Ensuring the integrity of pipelines transporting critical resources.
- Power Generation: Maintaining steam and cooling systems within power plants.
- Water and Wastewater Treatment: Designing effective and safe piping for municipal services.
- Pharmaceuticals: Upholding strict hygiene standards in production pipelines.
- Chemical Processing: Managing the stresses involved with transporting corrosive materials.
In each of these applications, a detailed understanding of pipe stress is key to maintaining operational reliability and safety.
Key Principles in Pipe Stress Analysis
Mechanical Properties and Loads Affecting Pipes
The mechanical properties of pipe materials, such as yield strength, tensile strength, and elasticity, play a significant role in their ability to withstand various loads. Additionally, understanding external loads, including wind, seismic activities, and thermal loads, is critical for accurate analysis. Each of these factors contributes to determining the safe operating limits of a piping system.
Engineers often utilize material specifications and standards (like ASME and ASTM) to ensure they select appropriate materials that can withstand the anticipated stresses.
Thermal Expansion and Contraction Considerations
One of the most important factors in pipe stress analysis is thermal expansion and contraction. As temperatures rise, materials expand; conversely, they contract when temperatures drop. If not properly accounted for, these movements can lead to pipe distortions, leaks, or even catastrophic failures.
Engineers consider factors such as thermal coefficients of expansion, temperature ranges, and the overall layout of piping systems to accommodate these changes. Properly designed expansion joints, bends, and supports can effectively mitigate the risks associated with thermal movements.
Calculating Stress: Methods and Tools Used
Several methods and tools are employed to calculate the stresses experienced by pipes. Finite Element Analysis (FEA) is one of the most commonly used computational techniques. FEA allows engineers to simulate how a pipe will react to various forces and conditions, providing valuable insights for design innovations.
Additionally, software programs such as CAESAR II, AutoPIPE, and ANSYS are widely used in the industry. These tools enable detailed modeling and stress analysis, making it easier to detect potential issues before they escalate into serious problems.
Choosing the Right Pipe Stress Company
Evaluating Experience and Expertise
When selecting a pipe stress company, it’s essential to evaluate their experience and expertise in the field. Look for companies that have a proven track record of successful projects and a deep understanding of industry standards.
A company’s qualifications and the experience of its team members—such as engineers and technical specialists—should be thoroughly assessed. Consider reviewing case studies or examples of previous work to gauge their capability in handling projects similar to yours.
Certifications and Compliance Standards
Certifications can provide assurance that a pipe stress company adheres to industry best practices and safety regulations. Check whether the firm is recognized by relevant industry bodies or holds certifications that demonstrate their commitment to quality and compliance.
Common certifications to look for include ISO 9001 for quality management systems and ASME standards, which are particularly important in the engineering sector.
Client Testimonials and Past Projects
Client testimonials and reviews can provide valuable insights into a company’s performance. Consider reaching out to previous clients to understand their experiences with the company. Discuss the quality of work, adherence to timelines, and communication throughout the project lifecycle.
Additionally, reviewing a company’s portfolio of past projects can illustrate their range of expertise and success in delivering effective solutions.
Best Practices for Successful Pipe Stress Analysis
Integrating Advanced Software Solutions
The integration of advanced software solutions into pipe stress analysis can significantly enhance accuracy and efficiency. Modern engineering tools facilitate sophisticated modeling, allowing engineers to visualize complex systems and predict stress responses under various conditions.
Using these software tools, engineers can simulate real-world scenarios, optimizing designs and identifying potential stress points long before construction begins. Organizations should prioritize investing in state-of-the-art software systems and providing ongoing training for their teams to leverage these technologies effectively.
Regular Maintenance for Long-term Safety
Regular maintenance and inspections of piping systems are crucial for ensuring long-term safety. over time, factors such as corrosion, material fatigue, and environmental changes can compromise the structural integrity of pipes.
Establishing a routine maintenance schedule helps identify potential issues early, allowing for timely repairs and replacements. Incorporating monitoring tools, such as sensors and automation technologies, can also enhance the effectiveness of maintenance efforts.
Collaborative Approaches with Design Teams
A collaborative approach between pipe stress analysts and design teams can significantly enhance project outcomes. Including pipe stress analysis in the initial design phase ensures that potential stresses are considered from the start, leading to more effective designs.
Encouraging open communication and collaboration between engineers, designers, and other stakeholders can also help identify and address potential concerns early, ensuring a streamlined workflow and minimizing costly changes or redesigns later in the project.
Future Trends in Pipe Stress Analysis
Emerging Technologies and Innovations
As technology advances, so too does the field of pipe stress analysis. Emerging technologies such as Artificial Intelligence (AI) and Machine Learning (ML) are starting to play a role in predicting stress points and optimizing designs. These technologies can analyze vast amounts of performance data, offering insights that were previously unattainable through traditional methods.
Additionally, the rise of cloud computing enables more extensive data storage and collaboration, allowing teams to work more effectively across various locations.
Impact of Industry 4.0 on Engineering Practices
Industry 4.0 is reshaping engineering practices by integrating smart technologies and the Internet of Things (IoT) into the pipeline ecosystem. This transformation allows for real-time data monitoring and analysis, enhancing the ability to predict and respond to stresses dynamically.
Pipe stress analysis will benefit significantly from data-driven approaches, as continuous monitoring allows for immediate adjustments and maintenance, further enhancing safety and reliability.
Preparing for the Future of Pipe Stress Management
Organizations must prepare for the future of pipe stress management by embracing technological advancements and fostering a culture of continuous improvement. Investing in training programs that familiarize engineering teams with new tools and methods will ensure a smooth transition into the evolving landscape of engineering.
Moreover, staying informed about industry trends and potential regulatory changes will allow companies to adapt quickly, maintaining their competitive edge while ensuring safety and compliance in their operations.