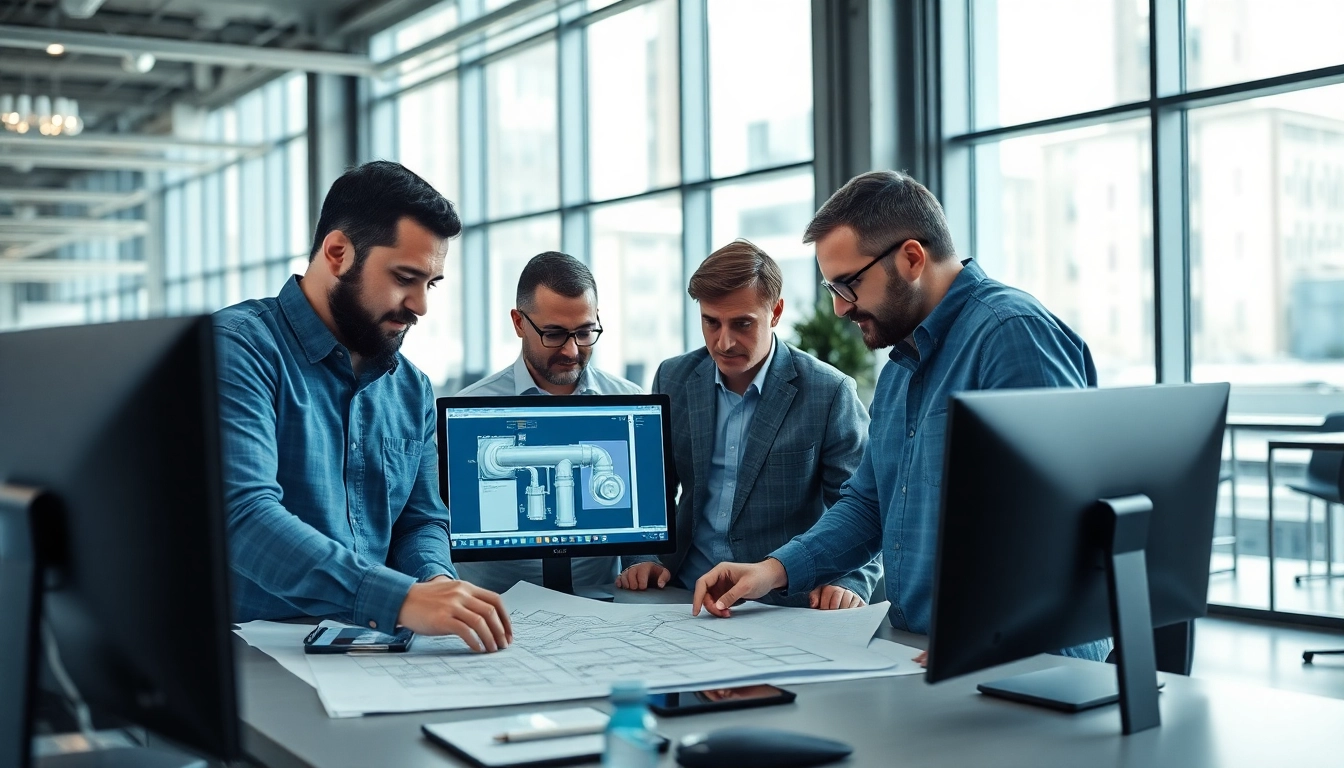
Understanding Pipe Stress Analysis
In the world of engineering, particularly in industries that deal with the transportation of fluids, the concept of pipe stress analysis is crucial. This process evaluates the stresses that occur in piping systems due to various loads and conditions, ensuring structural integrity and operational safety. To navigate this complex field effectively, many companies specialize in pipe stress analysis, offering valuable expertise to infrastructure projects. For those seeking a reliable pipe stress Company, understanding the fundamentals of pipe stress analysis is the first step toward enhanced safety and efficiency in engineering projects.
What is Pipe Stress Analysis?
Pipe stress analysis is the systematic evaluation of the stresses and strains that occur in piping systems under various conditions. These conditions include thermal expansion, weight of the piping and contents, pressure fluctuations, and external forces (such as wind or seismic events). The analysis aims to identify potential issues before they arise, allowing for design adjustments that improve safety and performance. Various methodologies, including simplified calculations and sophisticated simulations, contribute to comprehensive pipe stress analysis.
Importance of Pipe Stress Companies
Specialized pipe stress companies provide essential services to ensure that piping systems can handle operational stresses while complying with industry standards and regulations. Their expertise helps prevent failures that could lead to catastrophic events, financial loss, or environmental damage. By utilizing advanced techniques and tools, these companies offer insights that help engineers innovate safely, design efficiently, and maintain quality standards.
Key Factors Influencing Pipe Stress
The analysis of pipe stress is influenced by several critical factors. Understanding these can help engineers, designers, and project managers create safer and more effective piping systems. The key factors include:
- Material Selection: Different materials react differently under stress. The chosen material can significantly impact the overall resilience of the piping.
- Temperature Changes: Thermal expansion can lead to stress if not properly accounted for in the design.
- Fluid Characteristics: The type of fluid being transported can affect the pipe’s weight and the stresses it encounters.
- Support Locations: Where and how pipes are supported can change the distribution of stresses throughout the system.
- Operational Conditions: Changes in pressure, flow rates, and external forces can all introduce additional stresses.
Core Principles of Pipe Stress Engineering
Pipe stress engineering is grounded in fundamental principles that ensure piping systems are designed to withstand operational demands. Below are some core principles that guide engineers in pipe stress analysis.
Material Properties and Their Impact
The selection of materials used in piping systems is paramount. Properties such as yield strength, ductility, and thermal conductivity are critical considerations. For example, materials with high yield strength can withstand greater stresses but may be less flexible under dynamic loads. Conversely, ductile materials can absorb stress better but may deform under excessive force. The right balance is crucial for ensuring both safety and performance.
Thermal Expansion and Its Considerations
Thermal expansion is a significant factor in pipe stress analysis. As temperatures change, materials expand or contract, leading to potential stresses if not properly accounted for in the design phase. Engineers often incorporate expansion joints or flexible piping configurations to accommodate these changes and mitigate the risk of failure due to thermal stress.
Common Stress Analysis Methodologies
There are several methodologies employed in pipe stress analysis, each with its strengths and weaknesses. Common methods include:
- Simple Analytical Methods: These provide quick estimates of stresses and are useful for initial analyses.
- Finite Element Analysis (FEA): FEA allows for detailed simulations that can reveal localized stresses and potential failure points.
- Load Cases Evaluation: Different load cases, including dead loads, live loads, and dynamic loads, must be evaluated to assess the overall impact on the system.
Advanced Techniques Used by Leading Pipe Stress Companies
Leading pipe stress companies leverage advanced techniques to optimize their analysis processes and enhance the reliability of their results. The following sections explore these sophisticated methods in detail.
Finite Element Analysis (FEA)
Finite Element Analysis (FEA) is a powerful computational tool that enables engineers to explore how pipes behave under a wide range of conditions. By breaking down complex structures into smaller, manageable elements, FEA allows for a detailed examination of stress distribution throughout a pipe system. This method is particularly useful for identifying potential weak points and predicting how changes in design will affect overall performance. Its adoption among pipe stress companies is essential for high-stakes projects that demand rigorous safety standards.
Software Tools and Technology Trends
The evolution of software tools dedicated to pipe stress analysis has transformed how companies operate in this field. From CAD software that assists in the design phase to advanced simulation tools capable of performing real-time analysis, technology plays a pivotal role. Current trends show a movement toward integrated systems that allow seamless collaboration across engineering teams, ensuring that pipe stress considerations are consistently prioritized throughout the project lifecycle.
Case Studies of Effective Applications
Understanding the practical application of pipe stress analysis concepts can be beneficial. For instance, consider a large petrochemical plant where the cooling system’s piping was subjected to thermal fluctuations and high pressure. By employing a comprehensive stress analysis utilizing both FEA and traditional methodologies, engineers identified potential failure points in the system. Adjustments were made to support locations and material specifications, ultimately preventing a catastrophic failure during peak operation. Such case studies underscore the importance of robust pipe stress analysis in real-world applications.
Challenges Faced by Pipe Stress Specialists
The field of pipe stress analysis is not without its challenges. Specialists must navigate numerous obstacles while striving to deliver reliable solutions. The following sections discuss common challenges and effective strategies to overcome them.
Common Pitfalls and How to Avoid Them
In pipe stress analysis, pitfalls can lead to severe consequences, from design inefficiencies to system failures. Common mistakes include:
- Inadequate Consideration of Environmental Factors: Failing to account for site-specific conditions such as temperature variations and seismic activity can skew analysis results.
- Neglecting Dynamic Load Effects: Many analyses focus solely on static loads, ignoring dynamic conditions (such as vibration) that can significantly affect system performance.
- Overlooking Stress Concentrations: Recognizing areas of stress concentration is critical. Ignoring these can lead to early material fatigue and system failure.
Employing a thorough review process and leveraging experience can help mitigate these risks.
Regulatory Compliance and Standards
Regulatory compliance is an essential consideration for pipe stress specialists. Different countries and industries have specific codes and standards that govern piping safety and performance. Familiarity with regulations such as ASME B31.3 for process piping or API standards is critical to ensure that analyses are compliant. Maintaining updated knowledge of evolving standards also protects companies from potential legal and financial repercussions.
Managing Client Expectations
Managing client expectations effectively is crucial in pipe stress projects. Clients often desire rapid completion and cost-effective solutions, yet these factors can sometimes conflict with the thorough analysis required for safety. Clear communication about the specific needs for detailed analysis, potential project timelines, and associated costs helps align project goals and ensures client satisfaction.
Future Trends in Pipe Stress Industry
The pipe stress industry is continually evolving, influenced by advancements in technology and changing market demands. The following trends are shaping the future landscape of pipe stress analysis.
The Rise of Automation in Analysis
Automation is playing an increasingly important role in pipe stress analysis. Automated tools can expedite calculations and simulations, enhancing efficiency while reducing human error. The use of machine learning algorithms to predict material behavior under stress is also on the rise, enabling engineers to focus their expertise on more complex design challenges.
Increasing Demand for Sustainable Solutions
As industries move toward more sustainable practices, the demand for eco-friendly pipe materials and designs is growing. Pipe stress companies are increasingly tasked with developing systems that minimize environmental impact while ensuring structural integrity. This includes the use of recycled materials and innovative designs that reduce energy consumption.
Impact of Emerging Technologies on Practices
Emerging technologies such as artificial intelligence, augmented reality, and IoT are influencing how engineers approach pipe stress analysis. AI can optimize designs based on predictive modeling, while augmented reality provides enhanced visualization of piping systems during the design and maintenance phases. IoT devices can monitor real-time stress and strain data, allowing for proactive maintenance before issues arise.