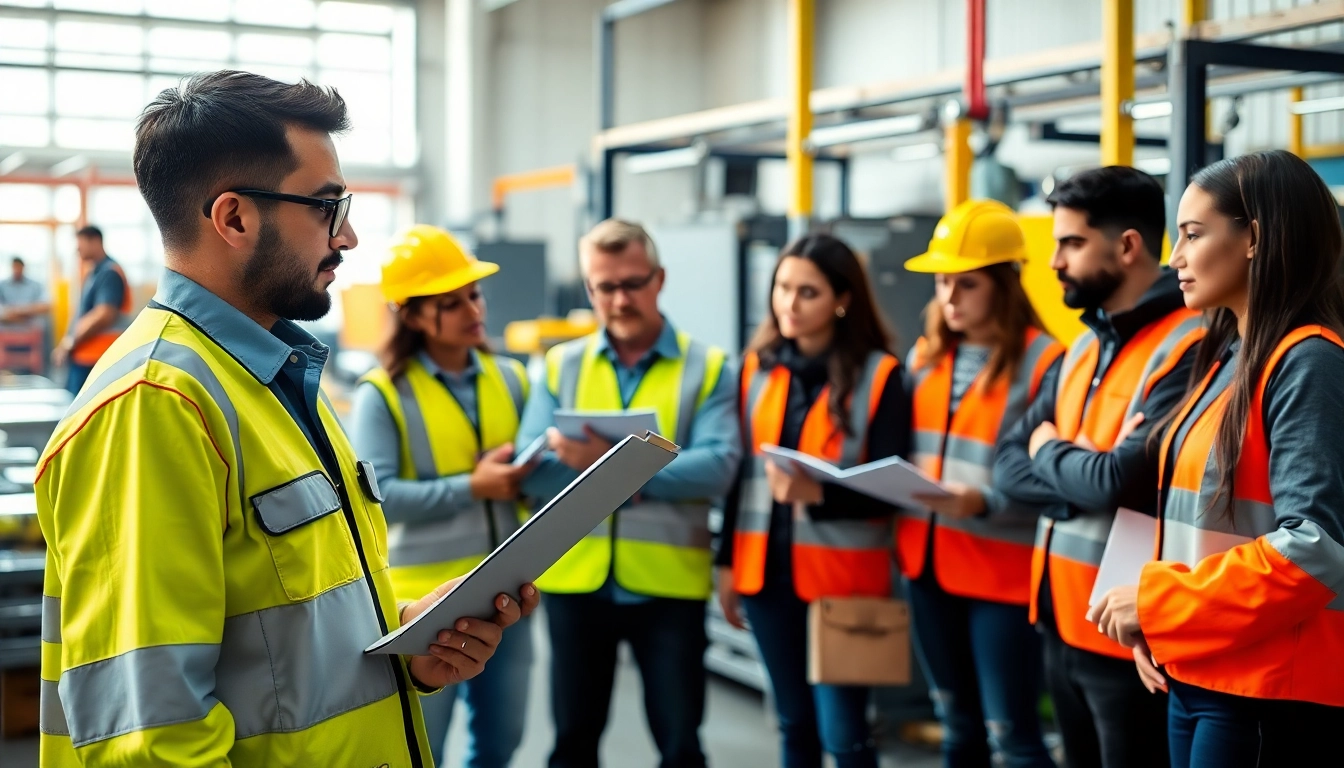
Understanding Workplace Hazard Assessment
Workplace Safety is paramount in ensuring that employees can perform their duties in an environment free from hazards. A comprehensive Workplace Hazard Assessment serves as a crucial tool for organizations, assisting in identifying risks and implementing measures to mitigate them. In this section, we will delve into the definition, importance, key components, and legal requirements surrounding workplace hazard assessments.
Definition and Importance of Workplace Hazard Assessment
At its core, a workplace hazard assessment is a systematic process designed to identify, evaluate, and control hazards in the workplace. The importance of conducting these assessments cannot be overstated. They provide a roadmap for enhancing workplace safety by ensuring that risks are systematically identified and addressed before they can cause harm. Regular assessments help prevent workplace injuries and illnesses, leading to increased employee morale, productivity, and retention rates.
Moreover, understanding and mitigating workplace hazards aligns with regulatory requirements, safeguarding organizations from legal liabilities and potential fines. Implementing an effective hazard assessment process fosters a culture of safety that not only protects employees but also boosts the organization’s reputation.
Key Components of a Hazard Assessment
Conducting a thorough hazard assessment involves several critical steps:
- Hazard Identification: This initial step involves documenting all potential hazards in the workplace, ranging from physical hazards such as machinery and equipment to health hazards like toxic substances.
- Risk Assessment: This involves analyzing the identified hazards to determine their potential impact on employee safety. Factors include the severity of the potential injury and the likelihood of occurrence.
- Control Measures: After identifying and assessing risks, the next step is to apply suitable control measures to mitigate the risks. This could include engineering controls, administrative changes, or personal protective equipment (PPE).
- Documentation: Keeping detailed records of all assessments, decisions made, and actions taken is vital for regulatory compliance and for reviewing and improving safety measures.
- Review and Continuous Improvement: Hazard assessments should not be static. Regularly reviewing and updating the assessments ensures they stay relevant and effective as workplace conditions evolve.
Legal Requirements and Standards
Various legal frameworks govern workplace safety regulations in the United States, with the Occupational Safety and Health Administration (OSHA) setting forth the primary standards that organizations must comply with. OSHA mandates that employers must properly assess workplace hazards and implement necessary controls to protect workers.
Additionally, state-specific regulations may impose further requirements, emphasizing the need for companies to stay informed about the laws that pertain to their operations. Regular reviews of compliance not only help maintain safety but also avoid potential legal repercussions.
Types of Workplace Hazards
Workplace hazards can be categorized into several types, each requiring tailored strategies for assessment and control. The following sections break down these categories.
Physical Hazards
Physical hazards refer to environmental factors that can cause harm without contact, including noise, temperature extremes, vibration, and illumination. Identifying these hazards is critical because they often lead to acute injuries or chronic health issues if left unaddressed. Common physical hazards include:
- Noisy Environments: Areas where loud machinery is used can cause hearing loss over time.
- Temperature Extremes: Workplaces with inadequate heating or cooling can result in heat stress or hypothermia.
- Inadequate Lighting: Poor lighting can lead to accidents and strain injuries.
Chemical Hazards
Chemical hazards encompass any chemicals that can pose a risk to health and safety. This includes substances that are flammable, toxic, corrosive, or reactive. Organizations must be vigilant in monitoring chemical hazards, given their potential to cause severe health issues ranging from respiratory problems to chemical burns. Key areas to focus on include:
- Material Safety Data Sheets (MSDS): Ensure that all chemicals have accompanying MSDS documents detailing their properties and safe handling instructions.
- Proper Storage: Chemicals should be stored according to their hazard classifications to prevent reactions or exposures.
- PPE: Evaluate and provide appropriate PPE to workers handling hazardous chemicals.
Biological and Psychosocial Hazards
Biological hazards involve exposure to living organisms that can cause infections, allergies, or disease. This category includes bacteria, viruses, fungi, and parasites. Workplaces such as healthcare facilities or laboratories often must pay closer attention to biological hazards.
Psychosocial hazards pertain to workplace stressors that can affect mental health and well-being. These may include workload stress, interpersonal conflicts, or workplace bullying. It’s crucial to recognize these hazards as their impact can lead to high turnover rates, absenteeism, and decreased productivity.
Steps to Conducting an Effective Hazard Assessment
Implementing a successful hazard assessment requires a structured approach. Below are the methodical steps organizations should follow to conduct effective hazard assessments.
Initial Preparation and Information Gathering
The first step in preparing for a hazard assessment involves gathering current information about the workplace environment, existing hazards, and previous assessment outcomes. Engage employees through surveys or interviews to get their insights on potential hazards they experience during their work.
Additionally, review regulations that apply to your industry and analyze past incidents to identify patterns that could indicate underlying hazards.
Conducting Inspections and Identifying Risks
Physical inspections of the workplace are crucial, utilizing checklists to systematically identify potential hazards. Employees from various departments should be involved in these inspections, as they bring unique perspectives and insights into their specific work areas.
During inspections, note the conditions in which employees work, safety equipment used, and any procedures that may contribute to risk exposure. Photographs and notes can be handy for documentation purposes.
Creating and Implementing Control Measures
After identifying risks, organizations must create tailored control measures that eliminate or reduce hazards. Control measures should be prioritized based on the level of risk they pose; for instance, implementing engineering controls (like safety guards on machines) should come before administrative changes (like rotas or training). Options might include the following:
- Engineering Controls: Modifying equipment or processes to minimize risks.
- Administrative Controls: Implementing policies or work practices that reduce exposure.
- PPE: Providing necessary personal protective equipment where risks cannot be fully mitigated.
Once the control measures are established, communicate and train employees on proper usage and procedures, ensuring clarity and compliance.
Common Challenges in Workplace Hazard Assessments
While conducting a workplace hazard assessment is critical, various challenges can arise, potentially hindering the effectiveness of the process.
Identifying Hidden Hazards
Hidden hazards can significantly jeopardize safety, as they may not be readily visible. Employers can adopt proactive measures such as regular audits and anonymous reporting systems to identify risks that may otherwise go unchecked. Training employees to recognize signs of potential hazards can also enhance proactive safety measures.
Engaging Employees in the Process
Employee participation is vital in conducting effective hazard assessments. Challenges may arise if employees feel their insights will not be taken seriously. To foster engagement, leaders should create an open forum for discussion regarding workplace safety, ensuring all employees feel valued. Recognizing and rewarding proactive safety involvement can also encourage participation.
Maintaining Compliance and Documentation
Maintaining accurate documentation and compliance with OSHA and other local regulations can be challenging, especially as workplace conditions change. To address this, companies should implement a digital safety management system that simplifies record-keeping and compliance tracking. This ensures that all documentation is readily available and compliant with current regulations.
Evaluating the Effectiveness of Your Hazard Assessment
Evaluating and ensuring the effectiveness of your hazard assessment process is essential in maintaining a safe workplace environment. This requires systematic monitoring and review strategies post-assessment.
Monitoring and Review Strategies
Employers should conduct regular follow-up assessments to ensure that implemented control measures are functioning effectively. Gathering feedback from employees regarding safety protocols and conducting random audits can help identify any weaknesses in controls. Implementing cultures of safety in the workplace ensures ongoing scrutiny regarding practices and conditions.
Adjusting Protocols and Training
As new hazards emerge or work processes change, it becomes vital to adjust safety protocols and training accordingly. Employers should regularly update training programs based on findings from workplace inspections and employee feedback to ensure they remain relevant and effective.
Reporting and Continuous Improvement
Organizations must maintain a system for reporting hazards or near misses, facilitating continuous improvement in safety mechanisms. Gathering data from incidents and analyzing trends can highlight areas for specific improvements. Furthermore, regular meetings to discuss safety can augment this reporting process.
In conclusion, a well-executed workplace hazard assessment is vital in promoting workplace safety and compliance. By identifying, assessing, and mitigating hazards effectively, organizations can foster a safer work environment that not only protects employees but also enhances organizational performance.