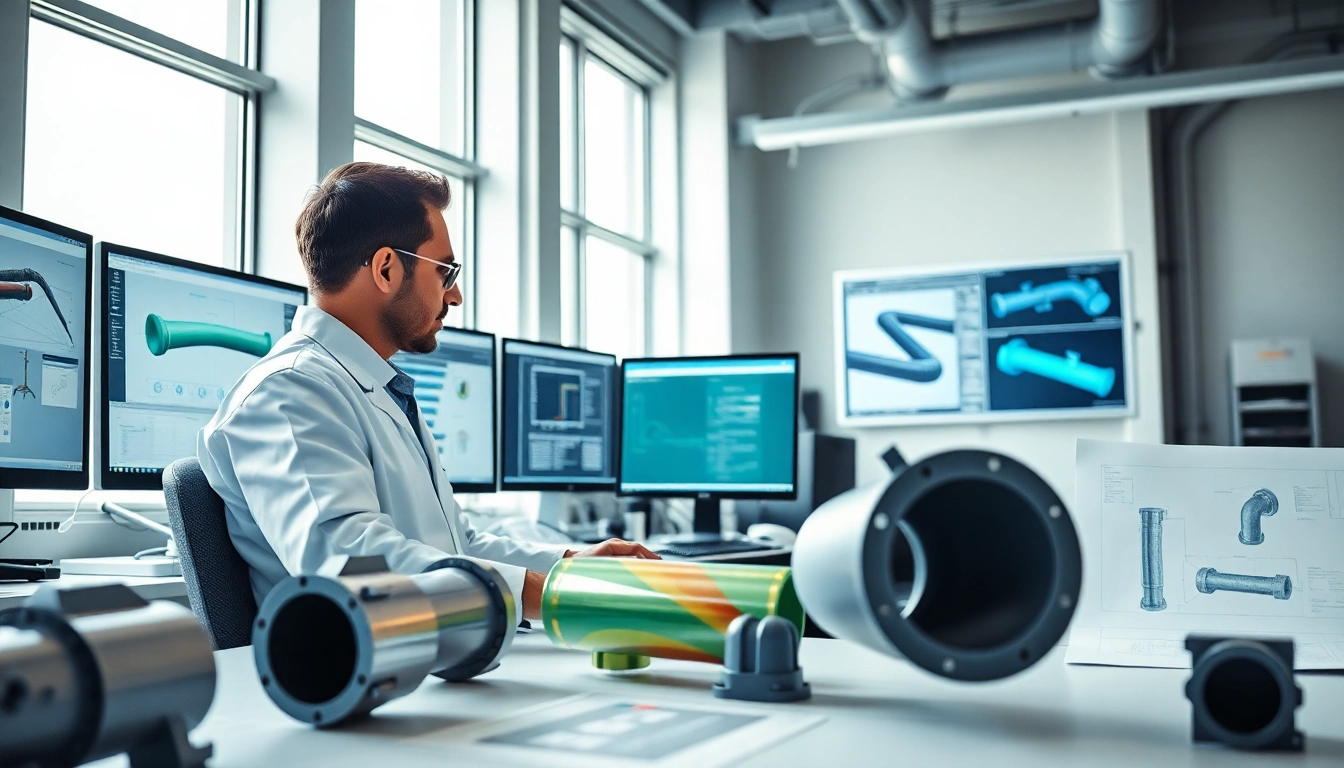
Understanding Pipe Stress Analysis
In the field of engineering, particularly in mechanical and civil engineering, pipe stress analysis plays a crucial role in ensuring the integrity and safety of piping systems. As piping forms an essential backbone for transporting fluids and gases in various industries, evaluating the stresses these systems endure under pressure, temperature fluctuations, and other operational conditions is imperative to avoid catastrophic failures. This article delves into the core aspects of pipe stress analysis, exploring its importance, underlying principles, types of stresses encountered, methodologies for conducting analyses, and the best practices for successful implementation.
What is Pipe Stress Analysis?
Pipe stress analysis is a form of engineering analysis employed to determine the stress and strain in piping systems under various external and internal influences. This analytical approach examines how piping behaves when subjected to forces such as internal pressure, temperature variations, dead weight, and dynamic impacts from environmental factors including seismic activity. The goal is to predict potential failure points or areas of excessive strain, enabling engineers to design systems that are both safe and efficient.
Importance of Pipe Stress Analysis in Engineering
The significance of pipe stress analysis cannot be overstated. It is vital for several key reasons:
- Safety Assurance: The foremost reason for conducting a pipe stress analysis is to protect human life and safeguard the environment. A failure in a piping system can lead to hazardous spills, explosions, or leaks of toxic substances.
- Compliance with Standards: Many industries are governed by stringent regulations and codes, such as ASME B31.3 for process piping. Pipe stress analysis helps ensure compliance with these standards, reducing legal risk.
- Optimization of Design: Analyzing stress conditions leads to more effective and economical designs. By understanding how piping behaves under different conditions, engineers can optimize pipe sizes, supports, and materials, ultimately reducing costs.
- Reliability and Maintenance: Through regular pipe stress analyses, engineers can predict when and where maintenance will be needed, boosting the reliability of the piping system and minimizing downtimes.
Key Principles of Pipe Stress Analysis
Several principles underpin effective pipe stress analysis:
- Load Types: Stresses in piping arise from different types of loads, including dead weight (the weight of the pipe and its contents), thermal expansion, and dynamic effects such as vibrations.
- Stress Criteria: It is crucial to understand allowable stress limits as defined by codes and standards. Typical criteria include yield strength, ultimate tensile strength, and fatigue limits.
- Support Analysis: The role of supports, hangers, and restraints in load distribution is paramount in preventing overstressing. The locations and types of supports directly affect the stress distribution along the pipeline.
- Temperature Effects: Thermal expansion leads to movement within pipe systems. Analysis must account for this to avoid stress concentrations that could lead to leaks or failures.
Types of Stresses in Piping Systems
Primary, Secondary, and Occasional Stresses
Understanding the different types of stresses encountered in piping systems is essential for a comprehensive analysis:
- Primary Stresses: These are direct results of the working conditions, including pressure and temperature. They are significant stresses that must not exceed specified limits to maintain safety.
- Secondary Stresses: These arise from thermal expansion and contraction, flexibility, and deformation under loads. Although they may be larger than primary stresses, they need to be evaluated in terms of fatigue life.
- Occasional Stresses: Occasional sources include extraordinary loads such as seismic events, water hammer, or pressure surges. These stresses are typically considered for short durations and are analyzed separately.
Calculating Different Types of Stresses
The calculation of stresses is achieved through various methodologies:
- Analytical Methods: These involve mathematical formulas derived from basic principles of mechanics. Stress can often be calculated using equations that account for loading and geometric parameters.
- Finite Element Analysis (FEA): This numerical method is powerful for complex geometries and loading conditions. FEA allows the simulation of how a pipe system behaves under applied loads, providing insights into stress distribution.
- Hand Calculations: For simpler systems or when checking results from more complex methodologies, hand calculations using fundamental engineering principles can still be effective for initial assessments.
Real-world Examples of Stress Types
In practical applications, different types of stresses can lead to specific failures:
- Fatigue Cracking: For example, pipes subjected to cyclic thermal loading may experience fatigue cracking due to secondary stresses over time.
- Buckling: In unsupported long spans or weak areas, primary stresses due to internal pressure can lead to buckling failures, especially in thin-walled pipes.
- Joint Failure: Occasional stresses that exceed allowable limits during seismic events can lead to joint failures, often resulting in catastrophic leaks.
Performing a Pipe Stress Analysis
Step-by-Step Guide to Conducting an Analysis
Conducting a pipe stress analysis involves several key steps:
- Define the Piping System: Gather all necessary details related to the piping configuration, materials, operating conditions, and load scenarios.
- Determine Load Cases: Include various conditions such as normal operating conditions, thermal movements, maintenance scenarios, and occasional loads.
- Select Analytical Method: Choose appropriate methods for calculation based on system complexity and accuracy requirements, whether analytical or with FEA.
- Model the System: Create a model of the piping layout in relevant software, replicating all dimensions and material properties diligently.
- Run the Analysis: Execute the stress analysis using the selected methodologies, applying loads as per predefined cases.
- Interpret Results: Analyze results to evaluate stress levels, comparing them against allowable limits specified by relevant codes.
- Document Findings: Prepare comprehensive reports detailing methodologies, findings, and recommendations for design adjustments if needed.
Common Tools and Software for Pipe Stress Analysis
Various tools exist to facilitate pipe stress analysis, optimizing both accuracy and efficiency. Some prominent software include:
- CAESAR II: Widely recognized for its robust capabilities in performing comprehensive pipe stress analysis.
- AutoPIPE: Known for integrating with other engineering software and delivering effective analysis within an intuitive user interface.
- PV Elite: Primarily focusing on pressure vessels, it also offers pipe stress assessment in conjunction with vessel analysis.
Interpreting Analysis Results Effectively
Data interpretation is crucial for deriving actionable insights from stress analysis results:
- Stress Ratios: Comparing calculated stress to allowable ranges helps in quickly assessing if the design is adequate.
- Visualizing Results: Utilizing graphical representations, such as contour plots, can enhance understanding of stress distribution across the piping system.
- Identifying Response Sensitivity: Analyzing how changes in design variables alter stress outcomes can provide insights for optimization.
Best Practices for Pipe Stress Analysis
Proven Techniques to Ensure Accuracy
Implementing proven techniques can significantly enhance the accuracy of pipe stress analysis:
- Detailed Input Data: Ensure that all parameters such as material properties, geometrical dimensions, and loading conditions are accurately defined.
- Regular Updates: Keep analysis software and models updated with the latest engineering practices and code revisions.
- Peer Review: Engage in regular peer reviews of analysis work to identify oversights and enhance the final output quality.
Common Mistakes to Avoid
Avoiding common pitfalls can streamline the analysis process:
- Neglect of Support Conditions: Underestimating the influence of support points on stress distribution can lead to unsafe designs.
- Ignoring Thermal Effects: Failing to account for thermal expansion can cause excessive stress in the piping systems, especially at high temperatures.
- Overlooking Occasional Loads: Neglecting to analyze occasional loads may leave vulnerabilities in the design.
Industry Standards and Compliance
Compliance with industry standards is critical in ensuring safety and efficacy:
- ASME Codes: Familiarity with relevant ASME codes such as B31.1 (Power Piping), B31.3 (Process Piping), and B31.4 (Pipeline Transportation Systems) is essential for any comprehensive analysis.
- ISO Standards: Following ISO standards can improve the sustainability and reliability of designs on a global scale.
- Safety Regulations: Staying updated with current safety regulations ensures ongoing compliance with district and state regulations which affect operational capacity.
Future Trends in Pipe Stress Analysis
Advancements in Software and Technology
The field of pipe stress analysis is continuously evolving. Key trends include:
- Increased Automation: Automation in design and analysis processes is becoming more prevalent, allowing engineers to focus on higher-level problem-solving.
- Cloud Computing: Leveraging cloud-based tools can enhance collaboration among engineering teams across different geographic locations.
- Integration with BIM: The integration of pipe stress analysis software with Building Information Modeling (BIM) facilitates comprehensive design and analysis.
Integrating AI in Pipe Stress Analysis
Artificial intelligence (AI) applications are beginning to impact pipe stress analysis:
- Predictive Analysis: AI can help predict failures before they happen by analyzing vast datasets from previous projects and real-time operating conditions.
- Optimization Algorithms: Leveraging AI for optimal design solutions can lead to more efficient piping systems with reduced material costs.
Impact of New Regulations on Stress Analysis Methods
As regulatory environments change, so too must methods of stress analysis. Future regulations are likely to place greater emphasis on:
- Sustainability Considerations: Future analyses will need to consider not just safety and compliance but also environmental impacts, which may reshape materials and operational limits.
- Increased Reporting Requirements: Enhanced documentation may be mandated, requiring more detailed analysis reports covering various aspects of design and operational safety.