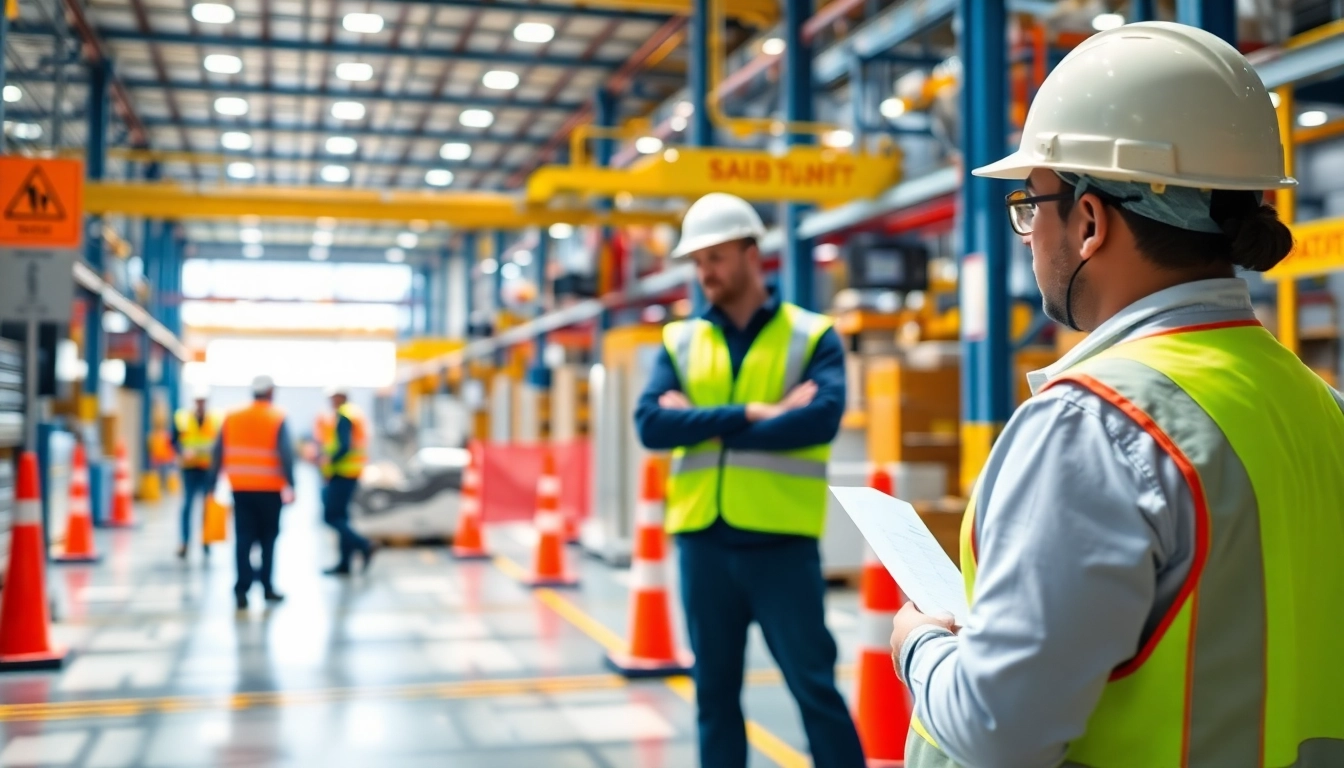
Understanding Workplace Safety Audits
Definition of Workplace Safety Audit
A Workplace Safety Audit is a systematic process designed to identify hazards and assess the risks present within a workplace. The audit evaluates whether existing safety measures align with applicable industry standards and regulations. This structured approach aims to collect vital information regarding the organization’s operational safety, reliability, efficiency, and effectiveness. It goads companies toward an environment that fosters both safety and accountability among employees.
Importance of Regular Audits for Business Safety
The significance of conducting regular safety audits cannot be overstated. These audits not only serve as compliance tools but also as preventive measures against occupational hazards. By identifying potential risks before they cause accidents, businesses not only comply with legal mandates but also demonstrate a commitment to the well-being of their employees. Furthermore, regular audits help identify areas for improvement, optimize safety procedures, and enhance overall working conditions, fostering a culture of safety and trust.
Components of a Comprehensive Safety Audit
A comprehensive safety audit typically includes various key components:
- Pre-Audit Planning: Defining the scope, objectives, and methods for the audit
- Documentation Review: Evaluating previous safety records and incident reports
- On-Site Inspection: Physically examining the workplace for hazards, unsafe practices, and compliance with safety standards
- Employee Interviews: Engaging with workers to gather insights about safety concerns and practices
- Reporting Findings: Documenting results and formulating actionable recommendations
Preparing for a Workplace Safety Audit
Steps to Prepare Your Team
Preparation for a workplace safety audit requires strategic planning. Here are key steps to consider:
- Inform the Team: Notify your safety team and relevant stakeholders about the upcoming audit well in advance.
- Review Past Audits: Go through previous audit findings and corrective actions to understand existing issues.
- Conduct Pre-Audit Training: Engage employees in training on what to expect during the audit.
Essential Documentation Needed
Gathering pertinent documentation is critical for an effective safety audit. Essential documents may include:
- Previous audit reports
- Incident and injury records
- Safety policies and procedures
- Training records
- Equipment maintenance logs
Setting Clear Audit Objectives
Establishing clear objectives for the audit helps direct the assessment process. Consider the following objectives:
- Evaluating compliance with safety regulations
- Identifying risks that could lead to incidents
- Improving safety culture within the organization
Conducting the Workplace Safety Audit
On-Site Inspection Techniques
The on-site inspection is a critical aspect of a safety audit, requiring various techniques such as:
- Walkthroughs: Physically traverse the workspace to examine conditions and practices.
- Safety Checklists: Utilize standardized safety checklists to ensure comprehensive coverage of inspections.
- Observation: Closely observe employee practices and safety behaviors in real time.
Identifying Hazards and Compliance Issues
During the inspection, it’s vital to accurately identify potential hazards and compliance issues. Common areas to assess include:
- Workstations: Evaluate ergonomics, layout, and equipment.
- Machinery: Check for proper maintenance and safeguards.
- Hazardous Materials: Inspect storage and usage practices of chemicals and other dangerous materials.
Engaging Employees in the Audit Process
Engagement of employees during the audit process is crucial. This can be achieved through:
- Conducting focus groups to gather employee perspectives on safety concerns.
- Encouraging open dialogue about observed hazards and safety practices.
Post-Audit Actions and Reporting
Documenting Findings and Recommendations
Documentation of audit findings must be thorough and clear. The report should include:
- A summary of the audit process
- Identified hazards and compliance issues
- Specific recommendations for corrective actions
Implementing Corrective Actions
Generating actionable recommendations is just the start; implementing them is crucial. Steps to take include:
- Prioritize recommendations based on risk level.
- Assign responsibilities for implementing each corrective action.
- Set deadlines for completion.
Communicating Results to Stakeholders
Effective communication of audit results is paramount, ensuring that all stakeholders understand the findings and proposed actions. This can be done through:
- Holding meetings with key personnel to discuss findings.
- Issuing written reports to all employees outlining the outcomes and next steps.
Evaluating the Impact of the Safety Audit
Measuring Effectiveness of Safety Improvements
After implementing corrective actions, it’s crucial to measure their effectiveness. Techniques include:
- Monitoring incident reports to assess changes in accident rates.
- Surveys to gauge employee perceptions of safety post-audit.
Continuous Improvement for Workplace Safety
A safety audit should be viewed as part of an ongoing process for improvement. Organizations should:
- Establish a routine schedule for audits
- Encourage feedback from employees to further refine safety protocols.
Feedback Mechanisms and Future Audits
Incorporating feedback mechanisms can enhance future audits. Suggestions include:
- Setting up suggestion boxes for continuous employee feedback.
- Conducting follow-up surveys to assess the culture of safety in the workplace.