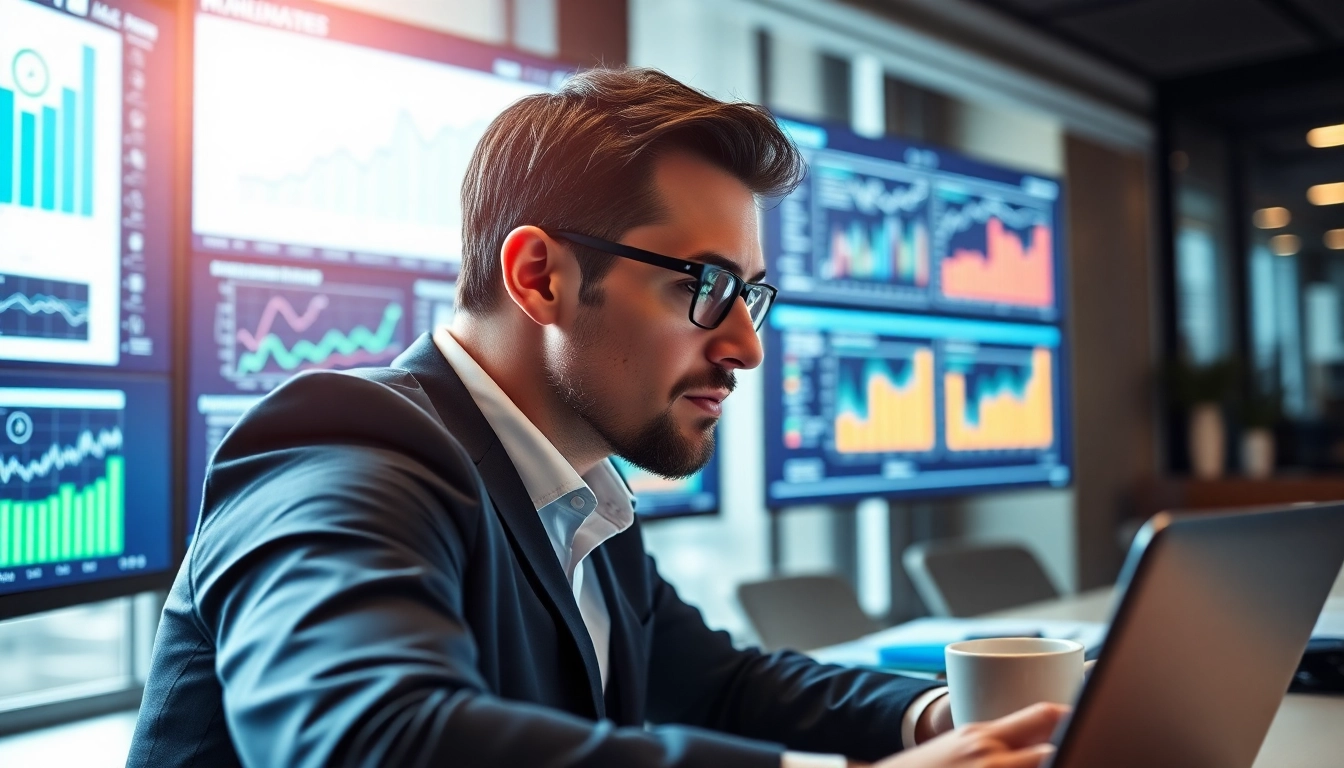
Understanding Process Optimization
Defining Process Optimization and Its Importance
Process optimization refers to the discipline of refining and enhancing an organization’s procedures to increase efficiency, improve performance, and reduce costs. This involves using various methodologies and tools to analyze existing processes, identify inefficiencies, and implement improvements. The importance of process optimization cannot be overstated. As global competition intensifies and technological advancements accelerate, businesses must adapt and evolve to remain relevant. An effective process optimization strategy not only streamlines operations but also enhances customer satisfaction, fosters innovation, and drives growth.
Key Principles of Process Optimization
When embarking on process optimization initiatives, several key principles should guide the approach:
- Customer Focus: Understanding customer needs is paramount. Processes should be designed to deliver maximum value to customers, ensuring their expectations are met and exceeded.
- Data-Driven Decision Making: Leveraging data analytics is crucial for identifying bottlenecks and inefficiencies. Informed decisions based on data help optimize processes effectively.
- Continuous Improvement: Optimizing processes is not a one-time event but an ongoing effort. Organizations should cultivate a culture of continuous improvement, where teams consistently seek ways to enhance their workflows.
- Collaboration: Engaging stakeholders across different departments is vital. Cross-functional collaboration fosters innovative solutions and a more holistic understanding of processes.
- Performance Metrics: Establishing and monitoring key performance indicators (KPIs) allows businesses to measure the effectiveness of their process optimizations and make necessary adjustments.
The Role of Technology in Process Optimization
Technology plays a pivotal role in modern process optimization efforts. From automation tools that streamline repetitive tasks to advanced analytics platforms that provide insights into performance, technology can significantly enhance efficiency. Emerging technologies such as artificial intelligence (AI) and machine learning (ML) allow organizations to predict trends and identify optimization opportunities more effectively. Moreover, cloud computing can facilitate real-time collaboration and data sharing, enabling teams to work more efficiently across geographical barriers. For companies looking to improve their process optimization, investing in the right technological tools is a critical step toward achieving their objectives.
Challenges in Implementing Process Optimization
Common Obstacles Businesses Face
Despite the clear benefits of process optimization, many businesses encounter various challenges during implementation. Some common obstacles include:
- Lack of Buy-In: Gaining commitment from all levels of the organization is critical. Resistance to change often arises if employees do not see the value or necessity of new processes.
- Insufficient Resources: Implementing process optimization initiatives typically requires a considerable investment in both time and money. Organizations may struggle to allocate sufficient resources to these efforts.
- Data Silos: Without integrated systems and open communication across departments, valuable data may remain isolated, leading to uninformed decision-making.
- Inconsistent Metrics: Organizations may have difficulty establishing consistent KPIs, which can hinder their ability to measure progress and success accurately.
Identifying Resistance to Change
Resistance to change is a natural response within organizations facing process optimization initiatives. Employees may fear job loss, feel overwhelmed by new systems, or believe that existing methods are sufficient. To identify resistance, organizations can conduct regular feedback sessions, surveys, and open forums, allowing employees to voice concerns. Awareness of this resistance is the first step toward addressing and alleviating it.
Mitigation Strategies for Implementation Challenges
To overcome barriers to successful process optimization, companies can employ several effective strategies:
- Leadership Engagement: Senior leadership should champion process optimization initiatives, modeling commitment and enthusiasm for change. Their support can inspire employees and foster buy-in across the organization.
- Training and Support: Providing comprehensive training and ongoing support equips employees with the necessary skills and knowledge to navigate new processes, reducing resistance.
- Clear Communication: Open lines of communication help keep all stakeholders informed about the goals, benefits, and progress of the optimization efforts, fostering transparency and trust.
- Incremental Changes: Instead of pursuing sweeping changes all at once, organizations can implement gradual adjustments. This approach minimizes disruption and allows teams to adapt more comfortably.
Best Practices for Effective Process Optimization
Conducting a Comprehensive Process Review
A thorough review of existing processes is a critical step in optimization. Organizations must map out current workflows, analyze them for inefficiencies, and identify areas for improvement. This often involves stakeholder interviews, observation, and process documentation. By understanding how processes function in practice, companies set the foundation for targeted enhancements.
Leveraging Data Analytics for Process Improvement
Data analytics provides invaluable insights that help organizations pinpoint inefficiencies and track improvements during optimization efforts. By gathering and analyzing process-related metrics, businesses can build a clear picture of performance. Important analytics might include cycle time, waste ratios, or defect rates. Organizations should establish data collection systems to ensure they have timely and relevant information at their fingertips.
Engaging Employees in the Optimization Process
Employees play a key role in successful process optimization. Engaging them in the process not only improves their ownership of improvements but also fosters a culture of collaboration and innovation. Encouraging team brainstorming sessions, establishing cross-functional teams, and creating incentive programs can motivate employees to contribute to optimization initiatives actively.
Real-World Examples of Successful Process Optimization
Case Study: Process Optimization in a Manufacturing Context
Consider a leading manufacturing firm that faced declining productivity due to outdated processes. By adopting Lean manufacturing principles, the company conducted a comprehensive review of its workflows. Implementation of just-in-time inventory practices and automation of repetitive tasks led to a 30% reduction in waste and a 25% increase in output within a year. This case illustrates how targeted optimization can significantly enhance operational efficiency.
Case Study: Enhancing Customer Service through Optimization
A well-known retail company aimed to improve its customer service experience. The organization analyzed customer feedback, and turnover metrics, and discovered that long wait times were a core issue. By streamlining call center operations through process automation and providing employees with data-driven insights, the company reduced call handling time by 40%, translating to higher customer satisfaction rates.
Lessons Learned from Leading Companies
Successful process optimization efforts from industry leaders offer several valuable lessons. First, the integration of technology must be strategic and aligned with business objectives. Second, fostering a culture that embraces change is essential; companies should encourage experimentation and tolerance for failure. Lastly, ongoing measurement and adjustment of optimization initiatives are critical to ensure continued success.
Measuring Success in Process Optimization
Key Performance Indicators to Consider
To effectively measure the success of process optimization initiatives, organizations should establish relevant KPIs, including:
- Cycle Time Reduction: Measuring the time taken to complete a task before and after optimization can illustrate improvements in efficiency.
- Cost Savings: Tracking direct costs associated with processes can help quantify the financial impact of optimization efforts.
- Quality Metrics: Assessing defect rates, customer complaints, or product returns provides insights into the quality enhancements following process changes.
- Employee Satisfaction: Monitoring employee engagement and satisfaction can reveal the impact of process optimizations on staff morale and retention.
Continuous Improvement and Process Optimization
To ensure long-term success, organizations must adopt a mindset of continuous improvement. This requires revisiting processes regularly, seeking feedback, and making iterative adjustments based on evolving business needs and insights from analytics. By nurturing a culture of improvement, organizations can remain agile and proactively address inefficiencies as they arise.
The Future of Process Optimization in Business
The landscape of process optimization is rapidly evolving, primarily driven by technological advancements. Artificial Intelligence and machine learning will further enhance process efficiencies by predicting trends and automating complex tasks. Additionally, as organizations shift towards remote and hybrid work models, optimizing digital workflows will become increasingly critical. To stay competitive, businesses must embrace these trends and adapt their process optimization strategies accordingly.