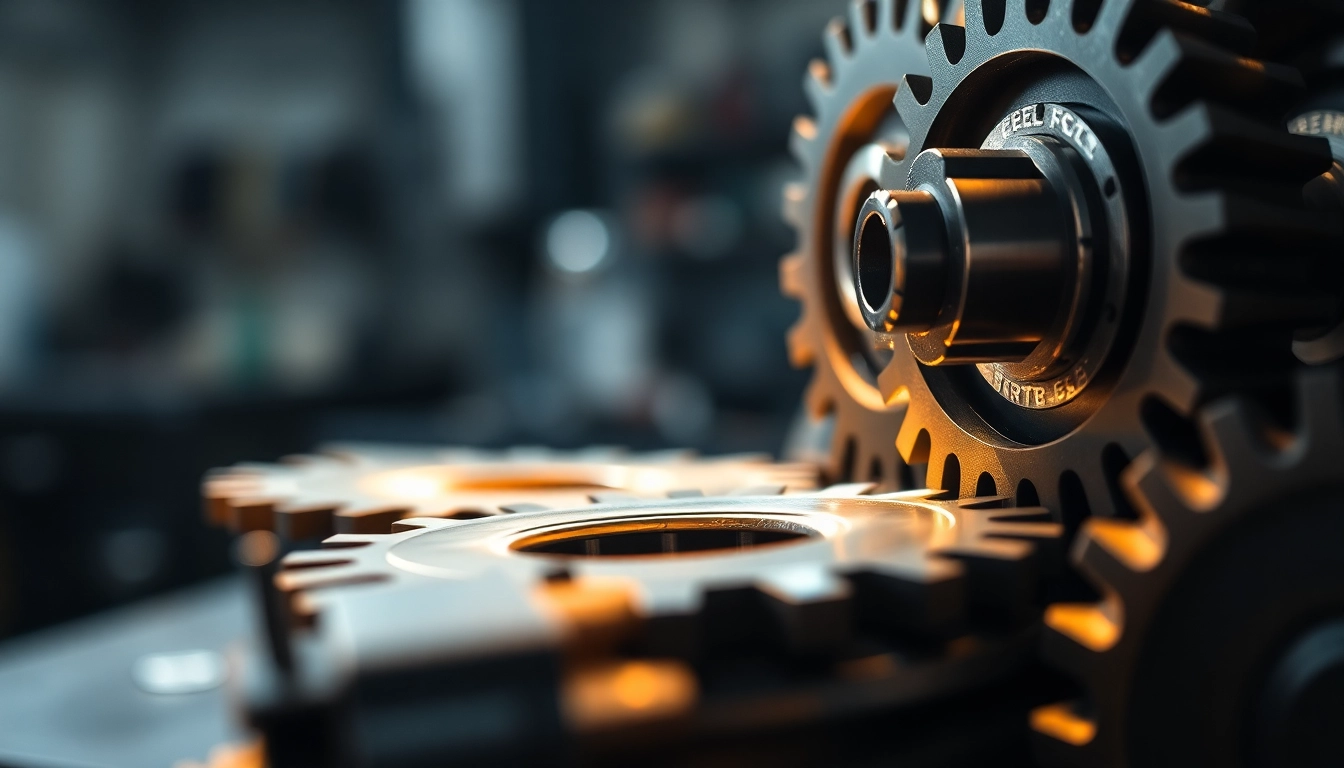
Understanding BYD Gears Basics
In the world of mechanical engineering and transportation, the role of byd gears cannot be overstated. These components are the backbone of various machinery, aiding in the conversion of rotational motion and the transmission of power. But what exactly are BYD gears, and why is their quality so crucial? In this section, we will explore the fundamentals of BYD gears, their significance, and the materials utilized in their construction.
What Are BYD Gears?
BYD gears are a type of mechanical component designed to transmit torque and modify rotational motion in devices ranging from electric vehicles to industrial machines. These gears can be classified into several types, including spur, helical, bevel, and worm gears, each serving unique functions depending on the application. They work by interlocking with one another, allowing for the smooth transfer of motion between machines while adjusting speed and force. Understanding the design and function of these gears is essential for anyone involved in industrial applications, automotive technology, or robotics.
The Importance of Quality in Gears
Quality in gears is imperative for the overall performance and reliability of machinery. Poorly manufactured gears can lead to increased wear and tear, inefficient energy usage, and ultimately, failure of the equipment. High-quality BYD gears ensure precision in movement and durability under stress. They are engineered to withstand varying loads and environmental conditions, thereby minimizing the risk of breakdowns and maintenance costs. In applications involving high speeds or significant weight loads, the importance of quality becomes even more pronounced, as subpar gears can pose serious safety risks.
Common Materials Used in BYD Gears
The manufacturing of BYD gears involves using various materials, each contributing different properties to the gear’s function and longevity. Common materials include:
- Steel: Known for its strength and durability, steel gears are often used in heavy-duty applications.
- Aluminum: Lightweight and resistant to corrosion, aluminum gears find applications in automotive and aerospace industries.
- Plastic: Used for quieter operation and lower friction, plastic gears are typically found in lighter machinery and consumer products.
- Composite Materials: A mix of different elements, composites are engineered for specific purposes, often providing enhanced performance characteristics.
Applications of BYD Gears
The versatility of BYD gears allows them to be applied across numerous industries, showcasing their importance in contemporary engineering practices. Below, we delve into various sectors that utilize these gears, along with innovative applications that highlight their adaptability.
Industries Utilizing BYD Gears
Several industries benefit from the use of BYD gears, including:
- Automotive: BYD gears play a critical role in electric vehicle (EV) technology, contributing to the efficiency of powertrains.
- Aerospace: In the aerospace sector, these gears are essential for the operation of components like landing gear and engines.
- Manufacturing: Gears are crucial in machinery for conveyors, milling machines, and robotic arms.
- Renewable Energy: In wind turbines and solar concentrators, gears help convert and manage energy efficiently.
Innovative Uses for BYD Gears
Aside from traditional applications, innovative uses for BYD gears are emerging. For instance, in robotics, gears are utilized in precise motion control, enabling complex maneuvers unachievable with simple mechanisms. In medical devices, they allow for accurate movements and control in surgical instruments. The integration of smart technology in gears is also on the rise, with sensors being embedded in gear systems for real-time performance monitoring.
Comparative Analysis of Gear Types
When discussing BYD gears, it’s essential to understand the different types available and their respective advantages. Each gear design serves a unique purpose, impacting performance. A comparative analysis reveals:
Gear Type | Advantages | Disadvantages |
---|---|---|
Spur Gears | Simple design, easily manufactured, efficient for parallel shafts | Can produce noise and vibration at high speeds |
Helical Gears | Operate more smoothly and quietly than spur gears, handle more load | More complex to manufacture, higher axial load |
Bevel Gears | Effective for transmitting power between non-parallel shafts | Can be difficult to align, may require precise installation |
Worm Gears | Provide high torque output, good for reducing speed | Lower efficiency, not suitable for high-speed applications |
Choosing the Right BYD Gears for Your Project
Selecting the correct BYD gears for a project can be vital to its success. The right choice not only improves performance but also extends the lifespan of equipment. This section outlines key specifications to consider, insights on matching gears to applications, and tips on selecting quality manufacturers.
Key Specifications to Consider
When choosing gears for a specific application, certain specifications must be taken into account, including:
- Gear Ratio: Determining the gear ratio is fundamental to understanding how speed and torque will be affected in a system.
- Material Strength: The material should withstand operational stresses. Factors such as tensile strength, hardness, and fatigue resistance are critical.
- Load Capacity: Gears must be selected based on the load they will handle to prevent premature failure.
- Operating Conditions: Consider environmental aspects such as temperature, humidity, and exposure to corrosive elements.
How to Match Gears to Applications
Matching gears to applications involves assessing the specific operational needs and challenges of a given project. Here’s how to ensure compatibility:
- Review the mechanical requirements, including force and speed requirements.
- Analyze space constraints, as the size of the gears will influence design choices.
- Consider the motion direction – for example, a shaft driving a conveyor belt will have different requirements than that of a motor in a pump.
Tips for Selecting Quality Manufacturers
Not all manufacturers produce quality BYD gears. Here are some tips to ensure you select a reliable source:
- Research manufacturers’ reputations and client reviews to gauge their quality standards.
- Look for certifications that indicate adherence to international manufacturing standards, such as ISO or AS9100.
- Assess their production capabilities and whether they can handle the specific requirements of your project.
- Evaluate after-sales support and warranty offerings to confirm ongoing reliability post-purchase.
BYD Gears Maintenance and Care
Regular maintenance of BYD gears is crucial for maximizing their lifespan and ensuring optimal performance. Proper care can mitigate common issues and enhance operational reliability over time. This section provides best practices for maintenance, troubleshooting tips, and strategies to enhance longevity.
Best Practices for Gear Maintenance
Implementing an effective maintenance routine can prevent malfunctions and extend the life of your BYD gears. Here are several best practices:
- Regular Inspections: Conduct routine checks to identify any wear, misalignment, or lubrication issues.
- Lubrication: Ensure that gears are adequately lubricated according to manufacturer specifications to reduce wear and friction.
- Cleaning: Regularly remove debris and contaminants that may interfere with gear operation.
- Monitoring Performance: Utilize monitoring tools to track the operational performance of gears and foresee potential issues.
Common Issues and Troubleshooting Tips
Despite preventive measures, issues may still arise with BYD gears. Here are some common problems and troubleshooting tips:
- Excessive Noise: Often indicates improper alignment or insufficient lubrication. Inspect and adjust accordingly.
- Overheating: Can result from inadequate lubrication or excessive load. Check for proper lubrication and evaluate load conditions.
- Wear and Tear: Monitor for symptoms like chipping or discoloration. Regularly replace gears that show significant wear to prevent equipment failure.
Enhancing Longevity of BYD Gears
Beyond immediate maintenance, several strategies can further enhance the longevity of BYD gears:
- Opt for higher-quality materials that provide superior fatigue resistance and durability.
- Incorporate advanced manufacturing techniques, such as heat treatment or surface hardening, for added strength.
- Utilize predictive maintenance technologies, allowing for data analytics to anticipate and address failures before they occur.
Future Trends in Gear Technology
The landscape of gear technology is constantly evolving, with emerging innovations and sustainability considerations becoming increasingly pertinent. This section explores cutting-edge developments in BYD gear design and what the future may hold for gear applications.
Emerging Innovations in BYD Gear Design
Recent advancements have sparked innovation in gear design, leading to improvements in efficiency and functionality. Some developments in BYD gear design include:
- Additive Manufacturing: 3D printing is transforming how gears are produced, allowing for complex shapes and custom designs that traditional methods cannot achieve.
- Smart Gears: Integration of IoT technology is enabling gears to communicate with other systems, providing data on performance and maintenance needs.
- Advanced Coatings: Development of high-performance coatings that improve wear resistance and reduce friction might significantly enhance the operational life of gears.
The Role of Sustainability in Gear Manufacturing
As industries strive for sustainability, gear manufacturing is also adapting. The future may see:
- Recyclable Materials: Increased use of recyclable metals and sustainable materials in gear production.
- Energy-Efficient Designs: Designing gears that contribute to the overall energy efficiency of systems, particularly in electric vehicles and renewable energy applications.
- Reduced Waste Production: Innovations in manufacturing processes aimed at minimizing waste and reducing carbon footprints.
Predictions for the Future of Gear Applications
The ongoing evolution of technology will continue to shape the applications of BYD gears. Expected trends include:
- Increased Automation: Gears will become integral components in more automated systems, including robotics and self-driving vehicles.
- Expansion in Renewable Energy Sector: The demand for efficient, high-performance gears in wind and solar energy systems will likely grow.
- Integration with AI: The combination of AI with gear systems will facilitate smarter operations, predictive maintenance, and enhanced performance monitoring.