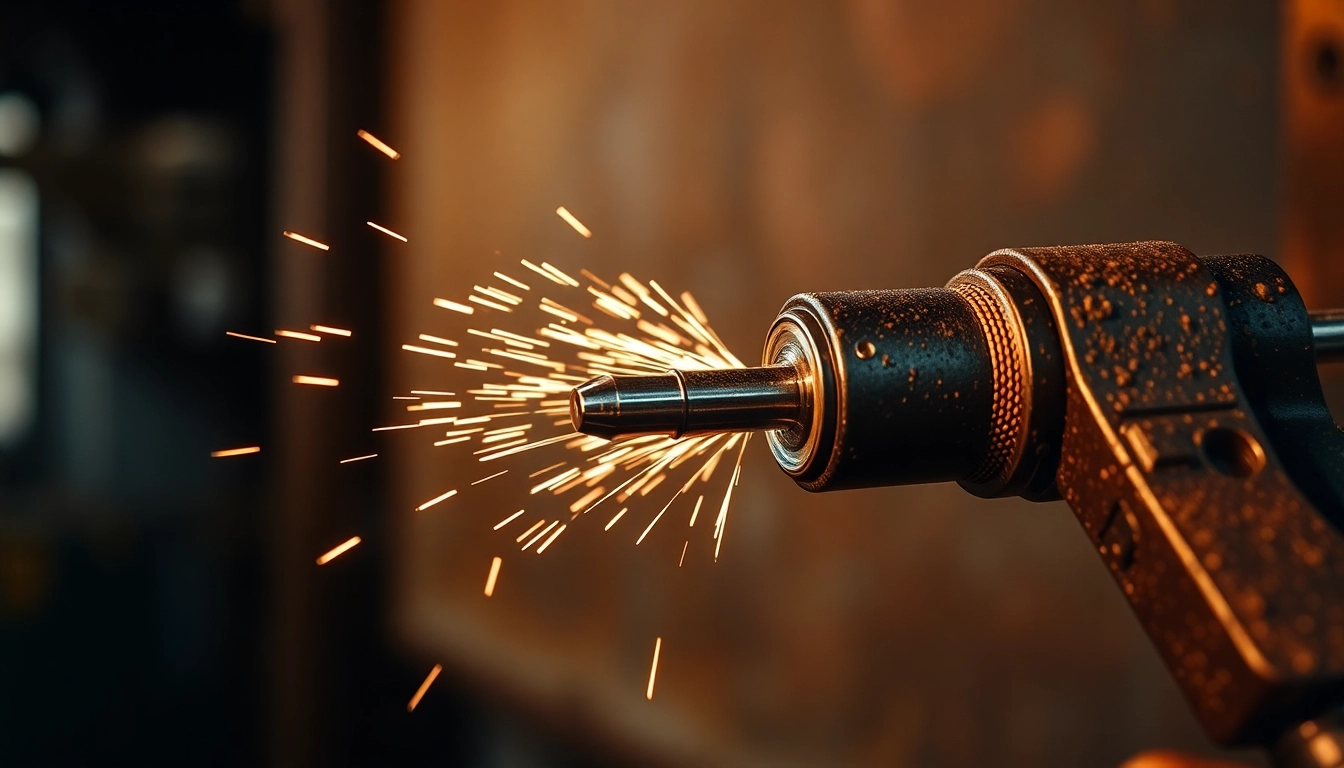
Introduction to Needle Guns
When it comes to surface preparation in various industrial applications, a needle gun stands out as a versatile tool tailored for efficiency. Known for its remarkable ability to remove rust, scale, and old paint from metal surfaces, the needle gun is an indispensable asset for professionals in metalworking, automotive maintenance, and more. In this comprehensive guide, we will delve into the intricate details of needle guns, their functionality, applications, and essential techniques for effective use.
Definition and Functionality
A needle gun, also referred to as a needle scaler, operates through a series of rapidly vibrating needles that strike the surface of the material being worked on. These needles penetrate and break up adhered materials such as rust, mill scale, or paint. The action is facilitated by a pneumatic mechanism, allowing for enhanced efficiency and precision during use.
Common Applications
Needle guns are predominantly used in environments that require thorough surface preparation, including:
- Automotive Repair: Used for cleaning and preparing surfaces before painting or welding.
- Metal Fabrication: Essential in industries where metal surfaces need to be cleaned for further processing.
- Marine Applications: Ideal for ship maintenance, particularly in removing corrosion and old paint.
- Home Restoration: Helpful in refurbishing metal furniture or equipment to restore their original finish.
Comparison with Other Tools
Compared to other surface preparation tools, such as sanders or grinders, needle guns offer the unique advantage of not only removing surface contaminants but also preserving the underlying material. While sanders can create a dust mess and may wear down the surface, needle guns limit damage to the metal while delivering efficiency in cleaning.
How Needle Guns Work
Mechanics of Needle Gun Operation
The operation of a needle gun relies fundamentally on compressed air that powers the rapid movement of needles. The needles are typically made from hardened steel and, during operation, are driven back and forth at high speeds. This hammering action effectively dislodges unwanted materials from the work surface. The effectiveness of a needle gun can be measured in strokes per minute (SPM), with premium models exceeding 4,000 SPM.
Pneumatic System Breakdown
Needle guns are primarily pneumatic tools. The main components of a pneumatic needle gun include:
- Air Compressor: Supplies the necessary compressed air to drive the tool.
- Air Hose: Connects the needle gun to the air compressor, transmitting air to power the device.
- Trigger Mechanism: Activates the needle movement when pressed, allowing for operational control.
- Needle Assembly: Comprises multiple needles that do the actual work of scaling and cleaning.
Safety Features and Precautions
While needle guns are relatively safe with proper handling, it’s essential to adhere to safety protocols:
- Personal Protective Equipment (PPE): Always wear safety goggles, gloves, and ear protection when operating a needle gun.
- Work Area Safety: Ensure your workspace is clutter-free, and avoid working near flammable materials due to metal particles created during the process.
- Tool Maintenance: Regularly inspect and maintain your tool to ensure its safe operation.
Choosing the Right Needle Gun
Types of Needle Guns Available
Needle guns come in various types, primarily categorized by their power sources:
- Pneumatic Needle Guns: These are powered by compressed air, typically offering higher power and efficiency.
- Electric Needle Guns: Battery or corded versions designed for portability, suitable for indoor uses or where air supply isn’t available.
Factors to Consider When Buying
When selecting a needle gun, consider the following factors:
- Power Source: Choose between pneumatic and electric models based on your specific needs.
- Needle Configuration: Look for the number of needles and their length, as this affects both the cleaning speed and surface condition post-cleaning.
- Weight and Ergonomics: Ensure the tool is lightweight and designed for prolonged use without causing fatigue.
- Noise Level: Consider options that operate at lower decibel levels if sound is a concern in your working environment.
Brand Comparisons and Recommendations
Several reputable brands manufacture needle guns, such as Ingersoll Rand, JET, and Von Arx. Customers should compare specifications, price points, and user reviews to make an informed decision. For example, Von Arx’s needle gun is known for its robust build and precision, making it a popular choice among professionals.
Techniques for Effective Use
Prep Work Before Use
Proper preparation is key to achieving optimal results:
- Inspect the Surface: Evaluate the condition of the metal surface and identify areas that require focused attention.
- Secure the Workpiece: Ensure the item being cleaned is stable and securely positioned to prevent accidents during operation.
- Adjust Equipment Settings: Configure air pressure settings according to the manufacturer’s recommendations for best performance.
Best Practices for Operating a Needle Gun
Efficiency during operation can be maximized by following these best practices:
- Angle of Approach: Maintain an appropriate angle when using the needle gun to maximize impact without damaging the surface.
- Movement Technique: Use a consistent and steady motion, overlapping passes to ensure thorough cleaning without leaving any spots.
- Timing: Avoid prolonged exposure on one area to prevent surface damage and allow for an even treatment.
Maintenance Tips for Longevity
To ensure longevity and optimal performance of your needle gun, consider these maintenance practices:
- Regular Cleaning: After each use, clean the tool to remove dirt and debris, especially from the needle assembly.
- Lubrication: Regularly oil moving parts as per the manufacturer’s guidelines to maintain efficiency and prevent wear.
- Inspection: Periodically check for any damaged needles or components and replace them promptly to avoid performance issues.
Advancements and Innovations in Needle Gun Technology
Electric vs. Pneumatic Needle Guns
The choice between electric and pneumatic needle guns often depends on the specific application. Pneumatic models are typically favored for heavy-duty tasks due to their superior power, while electric versions excel in portability and are ideal for light to medium-duty applications. Recent advancements in electric technology have produced battery-operated models that have comparable power to their pneumatic counterparts, broadening their usability in various situations.
Future Trends in Needle Gun Design
As industries move towards more sustainable practices, innovations in needle gun design focus on efficiency, reduced noise levels, and enhanced ergonomics. Future models may incorporate smart technology for pressure regulation and diagnostics to alert users about maintenance needs or performance issues.
Case Studies and Performance Metrics
Several case studies reflect the effectiveness of needle guns in real-world applications. For instance, in a recent project involving the restoration of a historic ship, the use of pneumatic needle guns reduced rust removal time by over 40% compared to traditional methods. Metrics such as surface cleanliness after treatment and time savings validate the machine’s efficiency, making them an invaluable asset in restoration projects.