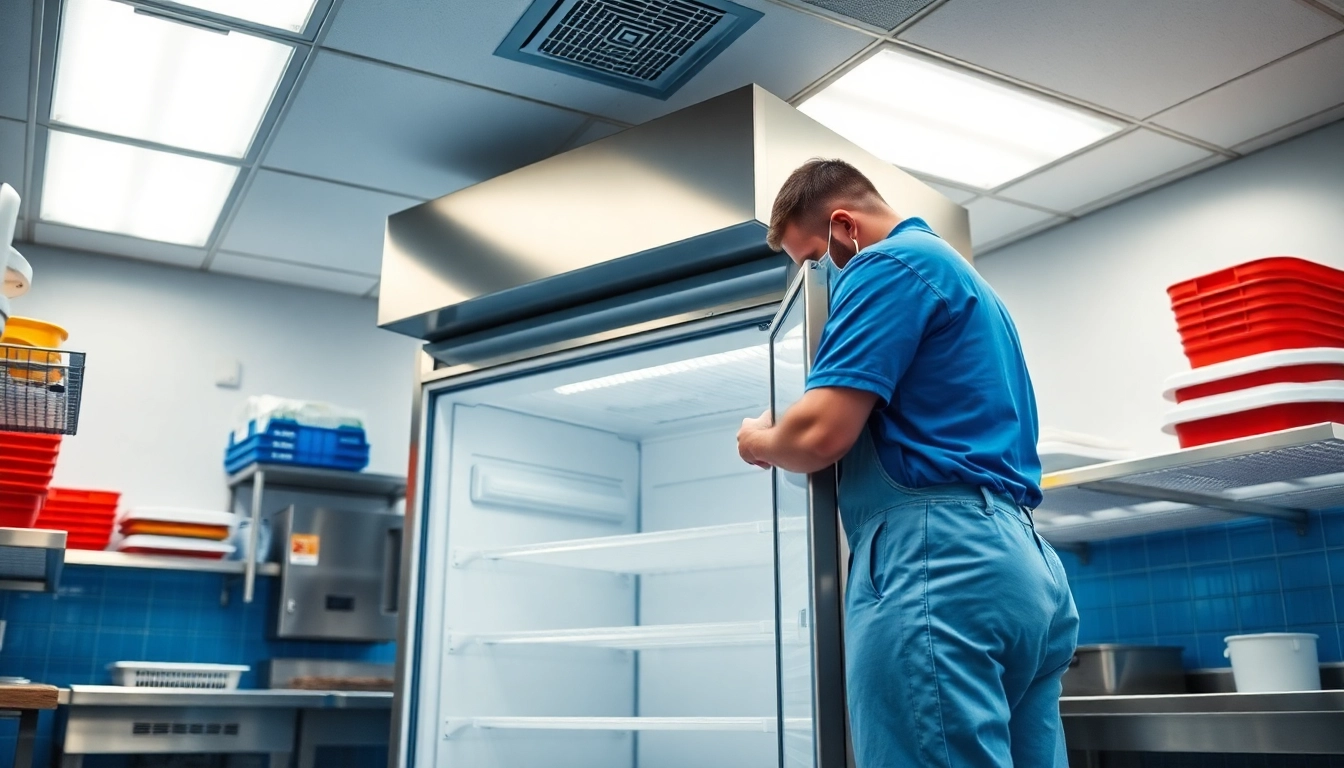
Understanding Walk In Cooler Repair Basics
Walk-in coolers are essential for many businesses, particularly those in the food service and retail sectors. When they malfunction, it can lead to significant losses due to spoiled goods. To minimize downtime and loss, understanding the basics of walk in cooler repair is vital.
Common Issues with Walk In Coolers
Walk-in coolers are complex systems that can experience various problems, often stemming from mechanical issues or improper maintenance. Some common issues include:
- Temperature Fluctuations: Inadequate cooling can occur due to issues with the thermostat, compressor, or refrigerant levels.
- Excessive Frost Build-Up: A malfunction in the defrost cycle or poor airflow can lead to frost accumulating on the evaporator coils.
- Strange Noises: Unusual sounds may indicate problems with the compressor or fan motors, leading to potential failures.
- Lack of Airflow: This often results from blocked vents, dirty filters, or malfunctioning fans.
- Odors: Unpleasant smells may indicate spoiled food or hygiene issues within the cooler.
Signs Your Walk In Cooler Needs Repair
Being proactive about identifying issues can save time and money. Common signs that your walk-in cooler needs repair include:
- Consistently high temperatures or temperature spikes.
- Ice accumulation on the evaporator coils or walls.
- Frequent cycling of the compressor.
- Unusual sounds like grinding or banging noises.
- Signs of leaks, including puddles of water near the cooler.
Importance of Timely Repairs
Timely repairs are critical for several reasons:
- Preventing Food Spoilage: A malfunctioning cooler can lead to spoiled inventory, directly impacting your bottom line.
- Energy Efficiency: Inefficient coolers require more energy, raising utility bills and harming your environmental footprint.
- Extending Equipment Lifespan: Addressing minor issues before they become major problems can prolong the life of your equipment.
- Maintaining Safety and Compliance: Regulatory bodies often have stringent requirements for food storage temperatures; failing to comply can result in fines or closure.
DIY Troubleshooting for Walk In Cooler Repair
Before calling a professional, some basic troubleshooting may resolve minor issues with your walk-in cooler. Here’s how you can start.
Initial Steps for Diagnosis
Begin by performing the following troubleshooting steps:
- Check the Power Supply: Ensure that the cooler is plugged in and that there are no tripped circuit breakers.
- Inspect the Thermostat: Confirm that the thermostat is set correctly and functioning properly.
- Evaluate the Refrigerant: If you suspect that the refrigerant is low, check for leaks and call a professional if necessary.
- Examine Airflow: Ensure that vents are not blocked and that air can circulate freely within the cooler.
- Look for Physical Damages: Inspect for any visible signs of wear or damage on seals, insulation, or structural components.
Tools Needed for Basic Repairs
Having the right tools can help you tackle minor maintenance or repairs effectively. Common tools include:
- Basic hand tools (screwdrivers, wrenches, etc.)
- Multimeter for electrical testing
- Pressure gauges for testing refrigerant levels
- Cleaning supplies (brushes, cloths, vacuum, etc.)
- Safety equipment (gloves, goggles, etc.)
Preventive Maintenance Techniques
Routine maintenance can prevent many issues. Incorporate these techniques to ensure your walk-in cooler operates efficiently:
- Regular Cleaning: Clean the interior and exterior of the cooler, including floors and shelves, to prevent mold and odor.
- Condenser Maintenance: Periodically clean the condenser coils to prevent overheating.
- Check Door Seals: Inspect and clean door seals to maintain energy efficiency and prevent air leaks.
- Monitor Temperature: Regularly check temperature readings to ensure proper function.
- Schedule Professional Inspections: Have a certified technician inspect the system annually for comprehensive maintenance.
Professional Walk In Cooler Repair Services
When issues exceed your capability, professional service may be necessary. Understanding how to choose and work with a service provider is crucial.
Choosing the Right Service Provider
Selecting a competent repair service is vital. Follow these guidelines:
- Credentials and Experience: Verify that technicians are licensed and have experience with walk-in coolers.
- References and Reviews: Look for testimonials or ask for references to gauge service quality.
- Service Range: Ensure they offer comprehensive services, including emergency repairs, maintenance, and replacements.
- Response Time: Evaluate how quickly they can respond to service calls, especially during emergencies.
- Cost Estimates: Request detailed estimates; understand the costs involved to avoid surprises.
Cost Factors in Professional Repairs
Understanding the costs associated with walk-in cooler repairs can prepare you for budgeting:
- Type of Repair: Simple repairs typically cost less than systemic issues that may require part replacements.
- Labor Charges: Rates can vary based on geographic location, technician expertise, and project complexity.
- Replacement Parts: Prices vary significantly; sourcing quality parts is essential for longevity.
- Emergency Services: Expect higher rates for after-hours repair requests.
- Maintenance Contracts: Consider these contracts as they often provide savings over one-time calls.
What to Expect During a Repair Service
Generally, professional repair services will follow a structured approach:
- Initial Assessment: Technicians will evaluate the equipment to identify issues.
- Diagnostics: They will perform tests to pinpoint the problem.
- Repair Proposal: A cost estimate and timeline will be presented before commencing repairs.
- Repairs: The technician will repair or replace the defective components or systems.
- Post-Service Checklist: After repairs, they will ensure the cooler operates correctly and meets applicable standards.
Walk In Cooler Repair Best Practices
Implementing best practices can enhance the performance and longevity of your cooler.
Routine Maintenance Strategies
Establish a routine that incorporates these key maintenance strategies:
- Regular Inspections: Schedule periodic inspections with a professional to catch issues early.
- Routine Cleaning: Establish a cleaning schedule focusing on the coils and filter systems.
- Inventory Management: Monitor the stock to avoid overloading the cooler, which can stress the system.
- Temperature Log: Keep a log of temperature checks to identify fluctuating temperatures quickly.
- Emergency Preparedness: Create a plan that includes alternative storage for perishable items in case of a breakdown.
Extending the Life of Your Cooler
To maximize the life of your walk-in cooler, consider these practices:
- Upgrade Components: Consider replacing older components with more efficient models to boost performance.
- Environment-Friendly Practices: Insulate and seal the cooler properly to minimize energy consumption.
- Training Staff: Educate your staff on the importance of proper cooler use and monitoring.
- Monitor Usage Patterns: Adjust settings based on high usage periods to better manage energy efficiency.
- Plan for Replacement: As your cooler ages, plan for potential replacements to avoid sudden failures.
Compliance with Health and Safety Regulations
Staying compliant with local health and safety regulations is essential. Follow these tips:
- Temperature Control: Maintain accurate temperature levels for food safety; typically, cold storage must be below 41°F (5°C).
- Documentation: Keep records of temperature monitoring, maintenance, and repairs for regulatory inspections.
- Food Safety Training: Ensure all employees are trained in the requisite safety regulations and proper cooler usage.
- Regular Inspections: Monitor compliance with health authorities through routine self-inspections.
- Prompt Repairs: Address any problems quickly to avoid penalties or fines.
Future Innovations in Walk In Cooler Technology
The refrigeration industry is evolving rapidly, bringing new technologies that enhance efficiency and reliability.
Latest Trends in Refrigeration Equipment
Stay up to date with innovations that could benefit your walk-in cooler system:
- Smart Temperature Monitoring: Newer systems offer integrated monitoring solutions that alert users to temperature changes.
- Energy-Efficient Designs: Innovations in insulation and design aim to reduce energy consumption significantly.
- Eco-Friendly Refrigerants: Advanced refrigerants are being developed to reduce environmental impact.
- IoT Integration: Internet of Things (IoT) technology allows for real-time monitoring and diagnostics.
- Automated Defrosting: Systems designed to self-regulate defrost cycles to minimize frost build-up and energy consumption.
Impact of Technology on Repair Needs
As technology evolves, so do repair needs:
- Diagnostic Tools: More advanced diagnostic tools can provide insights into problems before they escalate.
- Remote Access: Many new models allow service providers to access systems remotely to diagnose issues faster.
- Component Upgrades: As companies adopt new technologies, frequent updates to components may become necessary.
- Training Needs: Technicians need ongoing training to keep pace with technological advancements.
- Greater Availability of Parts: With newer technology, sourcing parts may either become easier or more challenging, depending on manufacturer support.
Preparing for Future Maintenance Challenges
To be prepared for future challenges, consider these strategies:
- Stay Informed: Keep abreast of new technologies and regulations affecting walk-in coolers.
- Invest in Training: Regularly train your staff in new systems and best practices.
- Create a Maintenance Routine: Adapt your maintenance strategies as new technologies are implemented.
- Build Relationships: Foster strong relationships with reliable service providers for timely support.
- Budget for Upgrades: Allocate funds for potential upgrades to equipment and technology.